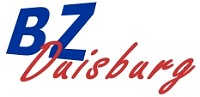
|
Redaktion Harald Jeschke |
|
Einsatz besonderer Art: Freiwillige Feuerwehr sammelt für
Kita Beeckerwerth |
Duisburg, 21. Dezember 2020 -
Wenn die Mitglieder der Löschgruppe 201 bei der
heilpädagogisch-integrativen Kindertagesstätte
Beeckerwerth in Duisburg vorfahren, drücken die Kinder an
den Fenstern schon voller Vorfreude ihre Nasen platt.
Denn die Feuerwehrleute haben dann nicht nur ihr rotes
Löschfahrzeug dabei, sondern auch gute Nachricht für die
Kita. Seit 1993 organisieren die Feuerwehrleute
Spendenaktionen für diese Kindertagesstätte, denn die
Kita Beeckerwerth im Duisburger Norden ist keine
Einrichtung wie jede andere. Hier finden auch schwerst-
und mehrfachbehinderte Kinder tagsüber ein zweites
Zuhause.
Die Ausstattung ist kostspielig und reicht vom
höhergelegten Sandkasten bis hin zur behindertengerechten
Matschanlage. Darum sammelt die Freiwillige Feuerwehr
seit 27 Jahren mit einem eigenen Förderverein Geld für
die Einrichtung des Deutschen Roten Kreuzes (DRK), in der
Kinder mit und ohne Behinderungen gemeinsam betreut
werden.
Der Stahlbereich von thyssenkrupp unterstützt die
Spendenaktionen seit vielen Jahren. Spenden, die gut
ankommen Die gespendete Summe kommt zu 100 Prozent der
Kita zugute. In den vergangenen Jahren erhielten die
Kinder zum Beispiel eine kind- und behindertengerechte
Außenanlage, spezielle Sitz- und Lesetischmöbel für
mehrfachbehinderte Kinder, die die Handhabung von Büchern
erleichtern, und eine Ferienfreizeit zusammen mit ihren
Eltern, die beide Seiten für den Alltag gestärkt hat. Im
vergangenen Sommer wurde die Kita um einen
außergewöhnlichen Raum erweitert: In einem feuerwehrroten
Bauwagen können die Kinder nun kreativ sein und malen,
basteln, ihre Fähigkeiten testen und ausbauen.
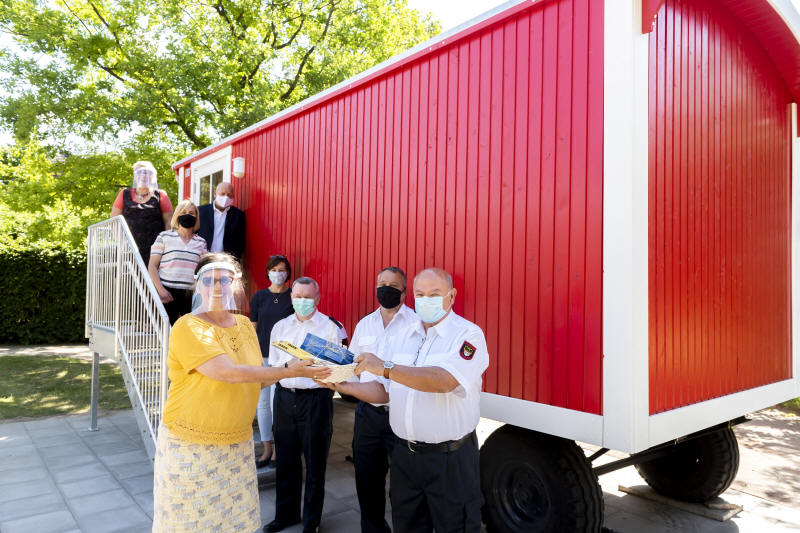
Durch Spenden ermöglicht: Im Sommer erhielt die Kita
Beeckerwerth einen feuerwehrroten Bauwagen, in dem die
Kinder kreativ sein und malen, basteln, ihre Fähigkeiten
testen und ausbauen können.
Möglich wurde all das durch die Spenden von Duisburger
Bürger*innen und Firmen. Auch in diesem Jahr sammelt die
Löschgruppe 201 für das nächste Projekt in der Kita. Für
die Spendenaktion KiTa2020 können alle Duisburgerinnen
und Duisburger gern spenden. „Wir freuen uns über jeden
Beitrag, damit wir gemeinsam an das schon Erreichte
anknüpfen können“, sagt der Vorsitzende des Fördervereins
der Freiwilligen Feuerwehr,Klaus Elshoff. „Denn die
Bedürfnisse dieser besonderen Kinder sind ganz einfach
und doch speziell: Sie wollen spielen, tanzen, lachen,
Bücher anschauen – wie andere Kinder auch.“ Diese ganz
normalen Dinge erfordern hier eine ganz spezielle
Unterstützung.
|
Grüner Wasserstoff für grünen Stahl aus Duisburg: STEAG
und thyssenkrupp planen gemeinsames Wasserstoffprojekt |
• Gemeinsame
Machbarkeitsstudie soll Grundlage für
Projektentwicklung und Wasserstoff-Hub schaffen •
Wasserelektrolyse auf STEAG-Gelände in
Duisburg-Walsum, basierend auf
Elektrolysetechnologie von thyssenkrupp
• Elektrolysekapazität bis zu 500 MW
• Lieferung von Wasserstoff und Sauerstoff für
thyssenkrupp Stahlwerk in Duisburg
• Projekt ermöglicht interessierten Investoren
Teilhabe an Wasserstoffwirtschaft
Duisburg, 03. Dezember
2020 - Das Essener Energieunternehmen STEAG, der
Duisburger Stahlhersteller thyssenkrupp Steel und
der Dortmunder Elektrolyseanbieter thyssenkrupp Uhde
Chlorine Engineers arbeiten an einer gemeinsamen
Machbarkeitsstudie. Gegenstand ist der Bau einer
Wasserelektrolyse am STEAG-Standort in
Duisburg-Walsum durch thyssenkrupp Uhde Chlorine
Engineers, die Strukturierung der Energieversorgung
und der Betrieb der Elektrolyse durch STEAG sowie
die Belieferung des Stahlwerks von thyssenkrupp
Steel im benachbarten Duisburger Stadtteil
Bruckhausen mit grünem Wasserstoff und Sauerstoff.
Die Studie soll eine Grundlage für die folgende
Projektentwicklung schaffen. Alle drei Parteien
planen eine Beteiligung als Investor und werden
gezielt private und öffentliche Finanzmittel
einwerben. Aufbau eines Wasserstoff-Hubs in NRW Die
kürzlich verabschiedeten Wasserstoffstrategien des
Landes NRW sowie die des Bundes und der Europäischen
Union heben die Bedeutung von Wasserstoff für eine
klimaneutrale Gesellschaft hervor. Sie unterstützen
den Aufbau einer Wasserstoffwirtschaft und
-infrastruktur in Deutschland und Europa.
Dem Land NRW und der Stadt Duisburg kann dabei eine
Schlüsselrolle zukommen: Hier ballen sich
Wasserstoffbedarf und technologische Expertise für
die Errichtung und den Betrieb von Elektrolysen. Die
Wasserstoff-Roadmap des Landes NRW verdeutlicht
diesen Anspruch und der Zusammenschluss von drei
Unternehmen aus der Region mit dem Ziel eines
lokalen Aufbaus einer Wasserstoffproduktion
unterstreicht diese Perspektive.
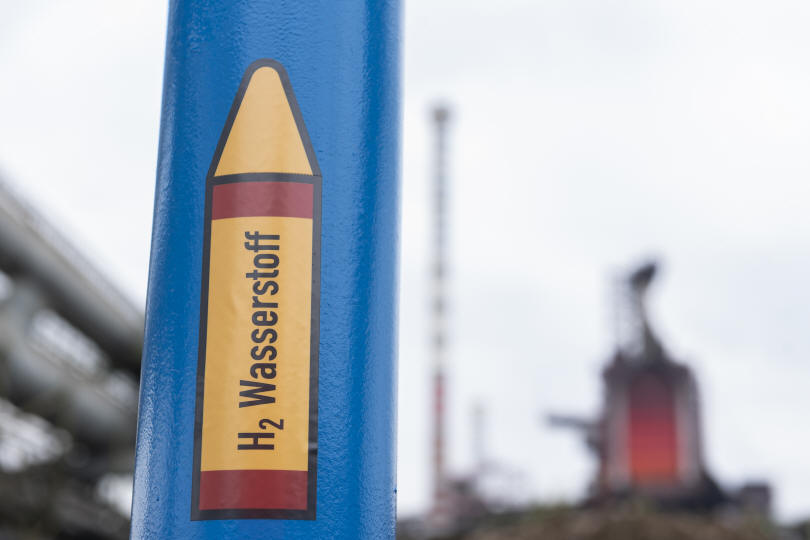
Wasserstoffeinsatz im Stahlwerk von thyssenkrupp
Wasserstoff ist der Schlüssel zur klimaneutralen
Stahlproduktion bei thyssenkrupp in Duisburg. Schon
heute erprobt das Unternehmen den Einsatz im
Hochofen. Im Hintergrund: Hochofen 8 in Duisburg
Hamborn. Quelle: thyssenkrupp Steel Europe
Kontinuierlich steigender Wasserstoffbedarf in der
Stahlherstellung thyssenkrupp Steel schafft durch
seine Klimastrategie in den kommenden Jahren einen
kontinuierlich steigenden und verlässlichen Bedarf
an grünem Wasserstoff. Dieser soll zunächst in den
bestehenden Hochöfen einen Teil des eingesetzten
Kohlenstoffs ersetzen und später in neuen
Direktreduktionsanlagen zum Einsatz kommen. Schon in
den kommenden Jahren rechnet das Unternehmen durch
die Umrüstung eines Hochofens mit einem Bedarf von
rund 20.000 Tonnen an grünem Wasserstoff pro Jahr.
Dieser Bedarf wird bis 2050 durch die schrittweise
Umstellung des Anlagenparks auf etwa 720.000 Tonnen
jährlich ansteigen.
Mit einer Leistung von bis zu 500 Megawatt (MW)
könnte die geplante Elektrolyse auf dem
STEAG-Gelände bereits bis zu rund 75.000 Tonnen
grünen Wasserstoff pro Jahr liefern – genug für die
erste Direktreduktionsanlage des Stahlherstellers.
Sie würde damit einen wichtigen Beitrag zur kurz-
und mittelfristigen Versorgung des Stahlwerks
leisten.
„Im Kern baut unsere Klimatransformation auf
Wasserstoff“, erklärt Dr. Arnd Köfler,
Produktionsvorstand bei thyssenkrupp Steel. „Er ist
der Schlüssel, um den großen Hebel umzulegen, den
wir bei der Senkung der CO2-Emissionen in der
Stahlindustrie haben. Dabei ist es wichtig,
frühzeitig zu planen. Wir müssen heute die Weichen
für die Versorgung stellen, um morgen klimaneutralen
Stahl produzieren zu können. Diese Zusammenarbeit
von drei Unternehmen aus der Region ist dabei ein
wichtiges Puzzleteil. Wir legen mit dem Projekt den
Grundstein für eine Wasserstoffwirtschaft in NRW.
Zudem geben wir mit dem Projekt Investoren die
Möglichkeit, direkt in diesen Wachstumsmarkt zu
investieren.“
STEAG-Gelände in
Duisburg-Walsum mit vielen Standortvorteilen
Die unmittelbare Nähe der Standorte ermöglicht eine
schnelle Anbindung ans Stahlwerk: Das Projekt
umfasst den Bau zweier neuer Pipelines für den
Transport von Wasser- und Sauerstoff von Walsum zum
weniger als drei Kilometer entfernt gelegenen
Stahlwerk. Ein Anschluss ans Höchstspannungsnetz
sichert die Versorgung mit grünem Strom für die
Elektrolyse; Großbatteriespeicher unterstützen die
Netzstabilität. Das etwa 15 Hektar große Gelände in
Duisburg-Walsum bietet die Möglichkeit,
Elektrolyseeinheiten bis zu einer Gesamtkapazität
von 500 MW zu errichten. Es verfügt zudem über eine
Anbindung ans bestehende Erdgasnetz, das
perspektivisch auch für den Transport von
Wasserstoff genutzt werden könnte. Doch nicht nur
die räumliche Nähe des STEAG-Areals spricht für das
Essener Energieunternehmen.
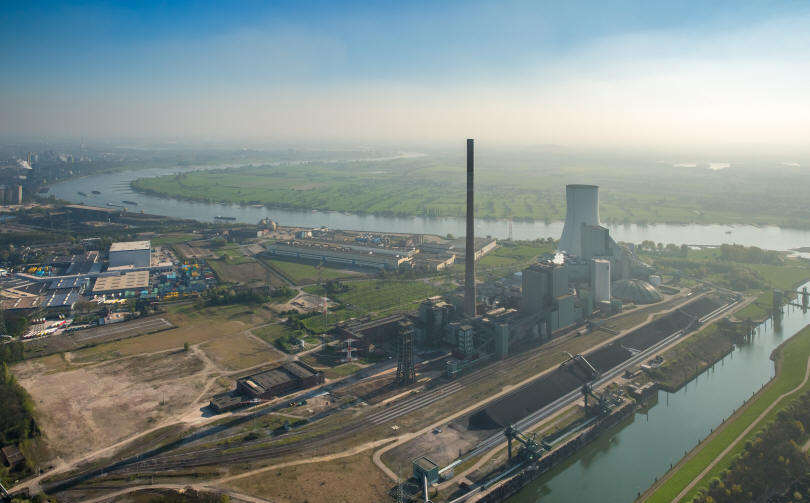
STEAG-Standort in Duisburg-Walsum Quelle: (C)
euroluftbild.de/Hans Blossey
Mit dem „HydroHub“ im saarländischen
Völklingen-Fenne, einer vom
Bundeswirtschaftsministerium in den Kreis der
„Reallabore der Energiewende“ aufgenommenen
Projektskizze, hat STEAG bereits Erfahrung in Sachen
Wasserstoffwirtschaft gesammelt.
„Das gemeinsame Projekt von thyssenkrupp und STEAG
hätte Signalwirkung für ein wichtiges Zentrum der
deutschen Industrie: Aufbau und Betrieb einer
Elektrolyseanlage in dieser Größenordnung sicherte
nicht nur langfristig den Stahl- wie auch
Energiestandort Duisburg sondern machte die Stadt
mit einem Schlag zur Keimzelle einer erfolgreich
florierenden, grünen Wasserstoffwirtschaft. Das hat
Strahlkraft über Duisburg und das Ruhrgebiet
hinaus“, sagt STEAG-Geschäftsführer Dr. Ralf
Schiele.
Duisburg werde so zu einem weltweiten
Leuchtturmprojekt in Sachen klimaneutraler
Stahlherstellung. Gleichzeitig ist das Projekt für
STEAG ein wichtiger Baustein im Rahmen der
strategischen Neuausrichtung des Unternehmens. Dabei
stehen der Ausbau des Geschäfts mit Energielösungen
sowie vermehrte Aktivitäten im Bereich der
Erneuerbaren Energien im Fokus.
Wasserelektrolysetechnologie aus dem Hause
thyssenkrupp:
Die Wasserelektrolyse wird von thyssenkrupp Uhde
Chlorine Engineers Produktbereich Green Hydrogen
installiert und setzt sich aus vorgefertigten
Standardmodulen zusammen. Durch dieses modulare
Konzept, lässt sich eine Anlage einfach auf bis zu
mehrere hundert Megawatt bzw. Gigawatt erweitern.
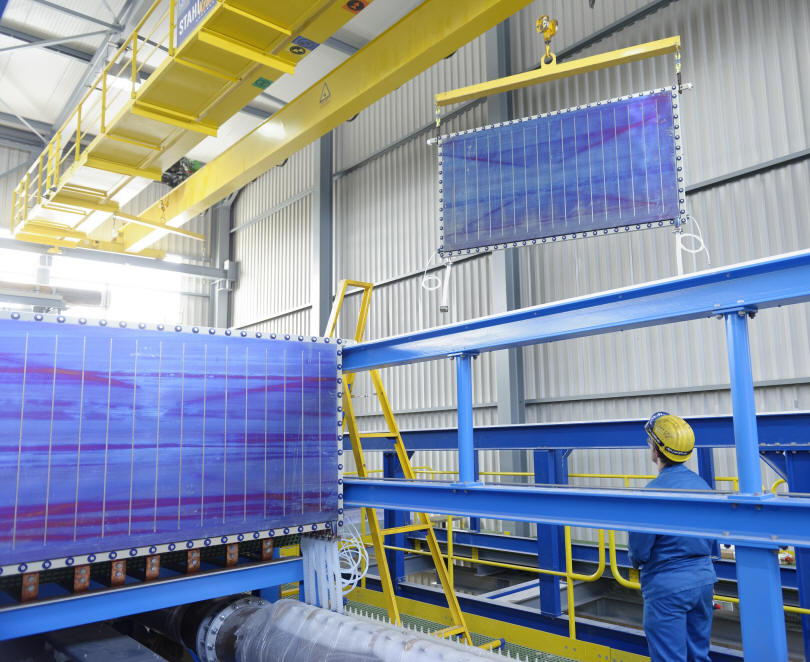
Modul Wasserelektrolyse Montage eines
Wasserelektrolyse-Moduls zur Herstellung von grünem
Wasserstoff. Quelle: thyssenkrupp Uhde Chlorine
Engineers
Dadurch ist der Einsatz für die Dekarbonisierung
über die grüne Stahlproduktion im industriellen
Maßstab hinaus vor allem auf dem Weg zu nachhaltigen
Wertschöpfungsketten und CO2-Reduktion interessant.
Diese Art der Sektorenkopplung ermöglicht neue
Geschäftsmodelle und eine nachhaltige
Kreislaufwirtschaft, die perspektivisch vollständig
durch erneuerbare Energiequellen gespeist werden
soll. Gemeinsam mit der Business Unit Chemical and
Process Technologies kann thyssenkrupp in Dortmund
somit die gesamte Palette grüner Chemikalien, von
Wasserstoff bis zu Ammoniak, Methanol und
synthetischem Erdgas, liefern, und so erheblich zu
einer klimaneutralen Industrie beitragen. Als
größtes Projekt seiner Art ist dies eine Blaupause
für den Export von Know-How und HighTech-Anwendungen
aus NRW in die Welt.
„Wir freuen uns sehr, uns mit unserer 50-jährigen
Erfahrung in der Planung, dem Bau und Betrieb von
Elektrolyseanlagen in diesem Projekt einbringen zu
können, um wettbewerbsfähigen grünen Wasserstoff im
industriellen Maßstab herzustellen“, sagt Sami
Pelkonen, CEO der Business Unit Chemical and Process
Technologies. „In dieser starken
Kooperationspartnerschaft können wir unsere
Spitzentechnologie aus der Region für die Region
nutzbar machen.“ Attraktives Projekt für Investoren
Das Projekt soll für Investoren geöffnet werden:
Neben der Beteiligung an der Projektentwicklung
können Investoren Anteile an der neu zu gründenden
Betreibergesellschaft erwerben.
Die Investoren finanzieren dabei gemeinsam mit den
Projektpartnern die Entwicklung und den Bau der
Wasserelektrolyse sowie die Anbindung an das
Stahlwerk und sichern sich durch die fixe Abnahme
von grünem Wasserstoff und Sauerstoff durch
thyssenkrupp Steel stabile Cash Flows. Die
geografische Nähe zum Abnehmer macht das Projekt
weitgehend unabhängig von Drittparteien und
ermöglicht eine schnelle Realisierung. Neben der
Öffnung für Investoren werden sich die
Projektpartner auch um öffentliche Fördermittel im
Rahmen der Beihilfen für klimaneutrale Technologien
bewerben.
|
Duisburger
SPD-Landtagsabgeordnete: „Ein Staatseinstieg bei
ThyssenKrupp Steel wäre ein Stabilitätsanker für die
NRW-Stahlindustrie!" |
Schock über drohendes Aus für das
Grobblechwerk in Hüttenheim Rainer Bischoff, AfA
Vorsitzender im UB Duisburg: "Schnelles Handeln
jetzt gefragt! "
Duisburg, 18. November
2020 - Die Duisburger
SPD-Arbeitnehmer sind entsetzt über die drohende
Schließung des Grobblechwerks in Hüttenheim. Nach
dem Absprung des letzten Kaufinteressenten will der
Thyssenkrupp-Konzern das Werk im Herbst 2021
schließen. „Das ist eine furchtbare Nachricht
für den Stahlstandort Duisburg“, so der Vorsitzende
der Duisburger SPD-Arbeitnehmer Rainer Bischoff,
„Wir als SPD-Arbeitnehmer fordern, dass die
Beschäftigten im Fall der Schließung des Werks,
schnell neue Angebote im Konzern erhalten. Sie
sollen nicht die Fehler der obersten Konzernetage
ausbügeln.“ Thyssenkrupp hat bis 2026 eine
Beschäftigungsgarantie gegeben, die auch die
Beschäftigten im Grobblechwerk miteinbezieht. Nach
Forderung der SPD-Arbeitnehmer sollen diese
Angebote, vor allem in Nähe um den jetzigen Standort
sein. „Die drohende Schließung des
Grobblechwerks zeigt sehr deutlich, dass ein
Staatseinstieg bei Thyssenkrupp dringend
erforderlich ist. Die Stahlbranche ist eine wichtige
Schlüsselindustrie für die Zukunft. Wir dürfen nicht
zulassen, dass der Stahlstandort Deutschland
wegbricht,“ sagt Rainer Bischoff.
Duisburg, 13. November
2020 - Die
ThyssenKrupp Steel Europe AG (TK Steel) steht seit
Jahren unter erheblichem wirtschaftlichen Druck.
Gründe dafür sind Überkapazitäten, wirtschaftliches
Missmanagement in der Vergangenheit und die
derzeitige Corona-Krise. Am heutigen Freitag wird
ein SPD-Antrag zur Staatsbeteiligung an dem Konzern
im Landtag NRW diskutiert. „Wir brauchen für unseren
Stahlstandort ein zukunftsfähiges Konzept“, fordern
die vier Duisburger SPD-Landtagsabgeordneten Rainer
Bischoff, Frank Börner, Ralf Jäger und Sarah
Philipp.
„Stahl ist die industrielle Lebensader für
Nordrhein-Westfalen und Duisburg. Stahl ist
systemrelevant“, so die SPD-Landtagsabgeordneten.
„Die Landesregierung muss Verantwortung übernehmen
und dafür sorgen, dass das Land Anteile von
ThyssenKrupp von mindestens 25 Prozent aufkauft, um
den Fortbestand zu sichern. Die Eigentümerseite und
die IG Metall haben sich bereits positiv dazu
geäußert. CDU und FDP müssen diese Chance nutzen und
ihren Worten Taten folgen lassen. Außerdem fordern
wir als SPD einen NRW-Stabilitäts- und
Transformationsfonds, damit sich andere Unternehmen
an ThyssenKrupp beteiligen können und der Konzern
weiter stabilisiert wird. Langfristig bedarf es
Investitionen in die Zukunftstechnologie
Wasserstoff.“
Direkt oder indirekt sind rund 100.000
Duisburgerinnen und Duisburger in ihrer Existenz vom
Überleben der Stahlproduktion betroffen. „Wir stehen
an der Seite der Beschäftigten bei ThyssenKrupp, die
auf hohem technischen Niveau engagiert ihre Arbeit
machen,“ so Frank Börner, Sarah Philipp, Rainer
Bischoff und Ralf Jäger. „Die kurzfristige
Stabilisierung von TK Steel Europe und die
mittelfristige Mitgestaltung der
Unternehmensstrategie sind von strategischer
Bedeutung für Duisburg und das Land NRW.“
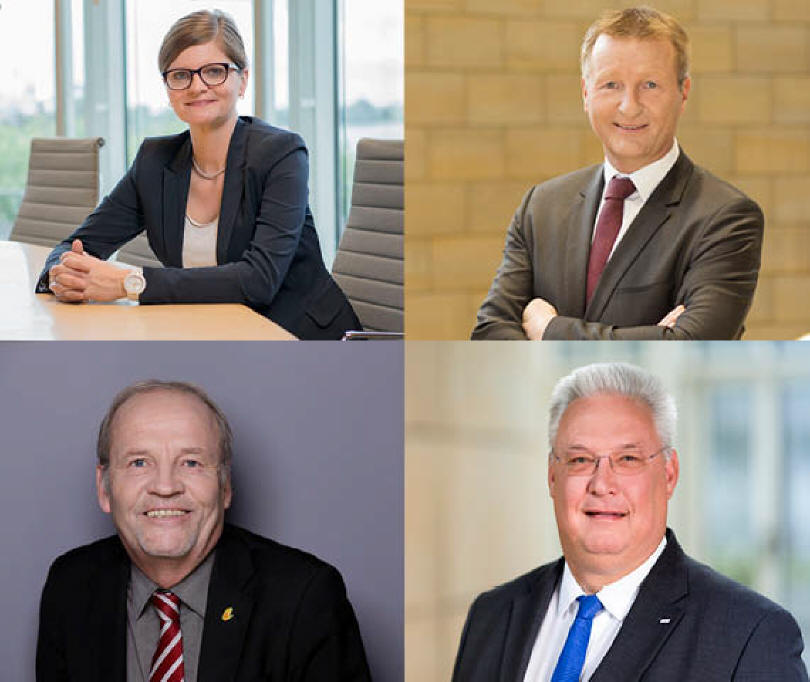
|
Carbon2Chem®: erste Projektphase erfolgreich
abgeschlossen und Förderbescheid des Bundes für zweite
Phase erhalten |
Erste Projektphase am
thyssenkrupp-Stahlstandort Duisburg demonstriert
technische Machbarkeit und bestätigt Wirtschaftlichkeit
Zweite Phase dient Ausweitung auf weitere Industrien
und Herstellung der Marktreife
Ministerin Karliczek überreicht Förderbescheid über 75
Mio. Euro für zweite Projektphase
Duisburg, 29. Oktober 2020 - Das von thyssenkrupp
initiierte Projekt Carbon2Chem® geht in die nächste
Phase. Gemeinsam mit 16 weiteren beteiligten Partnern hat
das vom Bundesministerium für Bildung und Forschung
(BMBF) geförderte Projekt in den vergangenen vier Jahren
grundlegende Erkenntnisse über die Umwandlung von
Prozessgasen aus dem Stahlwerk in chemische Produkte
gesammelt. Im nächsten Schritt geht es darum, die Lösung
auf weitere Industrien auszuweiten, die
Langzeitstabilität nachzuweisen und zudem die Marktreife
herzustellen. Dafür hat Bundesministerin Anja Karliczek
einen weiteren Förderbescheid über 75 Mio. Euro für den
Zeitraum bis 2024 überreicht.

Übergabe des Förderbescheids für Phase 2. v.l.n.r. Anja
Karliczek, Bundesministerin für Bildung und Forschung und
die drei Carbon2Chem-Projektkoordinatoren: Prof. Dr.-Ing.
Görge Deerberg, stellv. Institutsleiter des Fraunhofer
UMSICHT, Prof. Robert Schlögl, Direktor des
Max-Planck-Instituts für Chemische Energiekonversion und
Dr. Markus Oles, Head of Carbon2Chem bei thyssenkrupp
Steel Europe.
Copyright: Fraunhofer UMSICHT/Paul Hahn.
Entscheidende Phase abgeschlossen
2016 wurde das Projekt vom BMBF für die erste Phase
bereits mit mehr als 60 Millionen Euro gefördert. Seitdem
wurden wichtige Meilensteine erreicht: nachdem im März
2018 das Technikum in Duisburg die Arbeit aufnahm,
konnten binnen kurzer Zeit erstmals erfolgreich Ammoniak,
Methanol und höhere Alkohole aus Prozessgasen der
Stahlproduktion hergestellt werden. Neben dem CO2 aus
diesen Gasen nutzt Carbon2Chem® dazu auch Wasserstoff. Um
den Weg für eine klimaneutrale Produktion zu ebnen, wurde
im Technikum eine alkalische Wasser-Elektrolyse von
thyssenkrupp Uhde Chlorine Engineers mit einer Leistung
von zwei Megawatt betrieben.
Es wurde der Nachweis erbracht, dass die
Wasser-Elektrolyse auch mit sehr volatiler erneuerbarer
Energie betrieben werden kann, ohne Schaden zu nehmen.
Die Durchführung der chemischen Synthese mit kommerziell
verfügbaren Katalysatoren und der Betrieb der
Gasreinigung mit kommerziell verfügbaren Prozessstufen
durch thyssenkrupp Industrial Solutions bestätigt den
hohen technologischen Reifegrad (TRL) des Projekts. Zudem
wurde die Wirtschaftlichkeit sowie der positive
ökologische Effekt von allen Projektpartnern bestätigt.
Nächste Phase: Ausweitung und
Marktreife
In der jetzt gestarteten zweiten Projektphase wird es
darum gehen, nachzuweisen, dass die erarbeiteten Lösungen
im komplexen Zusammenspiel zwischen Stahlproduktion und
chemischer Synthese über lange Zeit stabile laufen und
die Carbon2Chem®-Technologie im industrieübergreifenden
Verbund sofort hochskaliert werden kann. Darüber hinaus
steht die Anwendbarkeit auf weitere Industrien neben der
Stahlherstellung im Mittelpunkt. So sollen zusätzliche
Sektoren als große CO2-Quellen in das Projekt aufgenommen
werden – etwa die Zement- und Kalkherstellung sowie
Müllverbrennungsanlagen.
Zuletzt soll die zweite Projektphase dazu dienen, das
Projekt zur Markreife zu führen. Für diesen nächsten,
wesentlichen Schritt ebnet die Förderung des
Bundesministeriums für Bildung und Forschung in Höhe von
75 Mio. Euro den Weg.
Anja Karliczek, Bundesministerin für Bildung und
Forschung: „Der Klimawandel ist eine der größten
Herausforderungen für die Menschheit. Wir müssen den
CO2-Ausstoß so schnell und effektiv wie möglich senken.
Bis 2050 wollen wir Europa zum ersten klimaneutralen
Kontinent der Welt machen. Das Projekt Carbon2Chem ist
ein Vorzeige-Beispiel dafür, dass wir diese
Herausforderung mit klugen Ideen und innovativer
Forschung erfolgreich meistern können. Denn mit den
Innovationen von Carbon2Chem schützen wir nicht nur das
Klima – wir stärken mit ihnen gleichzeitig unsere
langfristige Wettbewerbsfähigkeit und sichern hochwertige
Arbeitsplätze in der Industrie.“
Dr. Klaus Keysberg, Finanzvorstand der thyssenkrupp AG:
„Wir danken dem Bundesministerium für das Vertrauen und
die Unterstützung für unsere Klimatechnologien.
Carbon2Chem® kann gerade CO2-intensive Industrien auf dem
Weg zur Klimaneutralität unterstützen – das gilt nicht
nur für Stahl, sondern z.B. auch für die Zement- oder
Kalkproduktion. Wir sehen daher schon heute weltweites
Interesse an dieser Technologie. Mit der fortgesetzten
Förderung kann das Gemeinschaftsprojekt nun zur
Marktreife weiterentwickelt werden. In wenigen Jahren
bereits wollen wir Carbon2Chem® industriell einsetzen.“
Carbon2Chem® fester Bestandteil der
Dekarbonisierungsstrategie von thyssenkrupp
Bei thyssenkrupp Steel ist Carbon2Chem® auf dem Weg zur
klimaneutralen Stahlproduktion bereits fest eingeplant.
Neben der Vermeidung von CO2-Emissionen durch den Einsatz
von Wasserstoff zur Stahlproduktion setzt das Unternehmen
auf die Technologie, um anfallende Restemissionen nutzen
und vermeiden zu können. So soll Carbon2Chem® dazu
beitragen, die CO2-Emissionen im Hüttenwerk von
thyssenkrupp Steel bis 2030 um 30 Prozent zu senken und
bis 2050 vollständige Klimaneutralität zu erreichen.
|
thyssenkrupp Steel vergibt Auftrag zum Bau eines neuen
Hubbalkenofens am Standort Duisburg an Tenova |
Duisburg, 06. Oktober 2020 -
thyssenkrupp Steel hat den Auftrag zur Lieferung eines
Hubbalkenofens für das Warmbandwerk am Standort Duisburg
Beeckerwerth an Tenova LOI Thermprocess erteilt. Das
Unternehmen mit Sitz in Essen gehört zu den international
führenden Konstrukteuren von Industrieofenanlagen. Das
neue Aggregat soll für eine nochmals verbesserte
Oberflächenqualität bei Premiumblechen, die zum Beispiel
für die Außenhaut von Autos benötigt werden, sorgen. Vor
wenigen Wochen hatte thyssenkrupp die
Investitionsentscheidung zum Bau des Ofens getroffen.
Zum Vertragsumfang gehören das Engineering, die
weitgehend schlüsselfertige Lieferung aller Ausrüstungen
sowie die Supervision der Montage und Inbetriebnahme
inklusive Training für die Mitarbeiter. Der Ofen verfügt
über eine Kapazität von 380 t/h und wird in die
vorhandene Werksinfrastruktur eingebettet. Tenova liefert
die komplette Ofenanlage inklusive Chargierrollgang und
Chargiermaschine sowie die damit verbundene Elektro-,
Mess-, Steuer- und Regelungstechnik.
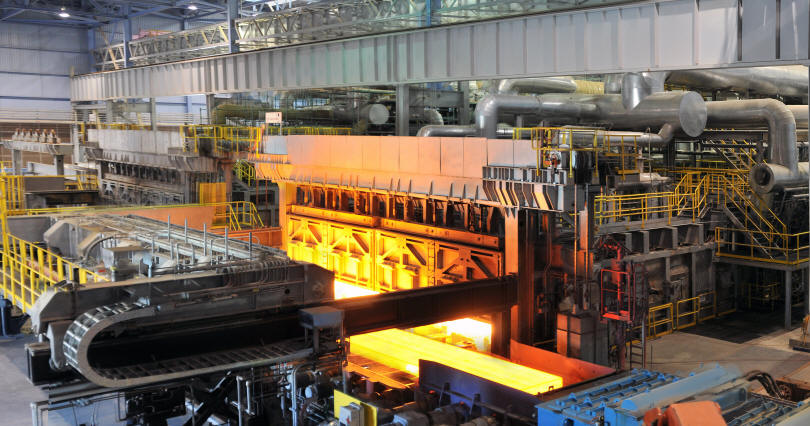
tenova Hubbalkenofen. Ein baugleiches Aggregat wird nun
im Warmbandwerk am Standort Duisburg installiert.
Der neue Hubbalkenofen wird eine
Verbrennungsluftvorwärmung erhalten, die den
Energieverbrauch im Warmbandwerk deutlich absenken wird.
Ein anspruchsvolles Automatisierungssystem trägt darüber
hinaus zur zuverlässigen Steuerung und Energieeffizienz
bei. Die Anlage ersetzt ein älteres Aggregat und wird
direkt neben einem bereits vorhandenen, ebenfalls von
Tenova gelieferten Hubbalkenofen aufgestellt.
„Wir haben uns aufgrund der Vielzahl
an Referenzen für vergleichbare Anlagen für Tenova
entschieden“, erläutert Dr. Arnd Köfler,
Produktionsvorstand bei thyssenkrupp Steel. „Die kurze
Realisierungszeit ist ein weiteres wichtiges Kriterium.
Mitte 2022 soll die neue Anlage den Betrieb aufnehmen.“
|
300 neue Auszubildende starten bei der thyssenkrupp Steel
Europe AG in Duisburg, Bochum, Dortmund, Finnentrop und
Kreuztal
|
Duisburg,
03. September 2020 -
300 junge Menschen haben am 1. September eine Ausbildung
an den Standorten der thyssenkrupp Steel Europe AG
angefangen. „Gerade in diesem Jahr freuen wir uns ganz
besonders auf unsere neuen Kolleginnen und Kollegen und
wünschen ihnen einen guten Start bei uns“, sagt Volker
Grigo, Ausbildungsleiter bei der thyssenkrupp Steel
Europe AG. „Auch in Corona-Zeiten bieten wir jungen
Leuten an unseren Standorten konstant eine Ausbildung in
unserem Hause an. Denn wir sind davon überzeugt, dass
unsere NachwuchsSteeler mit einem unserer 22
Ausbildungsberufe auf jeden Fall bestens gerüstet sind
für ihre berufliche Zukunft.“
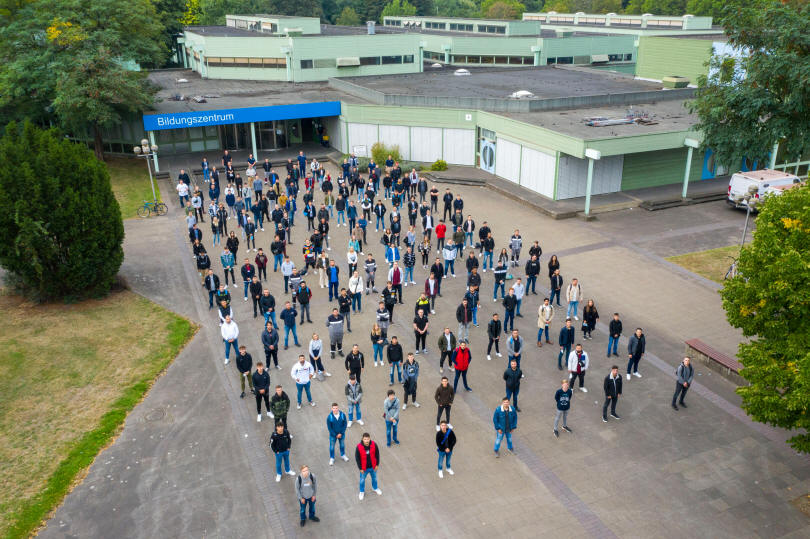
Gemeinsam, aber mit Abstand:
In der Stahlsparte von thyssenkrupp haben am 1. September
300 junge Menschen ihre Ausbildung angefangen, 193 davon
in Duisburg (hier im Bild). Am stärksten vertreten sind
die Industriemechaniker.
Industriemechaniker größte Ausbildungsgruppe
Auch in diesem Jahr bilden die Industriemechaniker die
größte Ausbildungsgruppe, gefolgt von den Elektronikern
für Betriebstechnik und den Verfahrenstechnologen mit der
Fachrichtung Stahlumformung.
Oguzhan
Öncü, hat seine Ausbildung als Verfahrenstechnologe,
Fachrichtung Metallurgie am Standort Duisburg begonnen
und fühlt sich an seinem dritten Tag bei thyssenkrupp
angekommen.
„Nach dem Abitur habe ich angefangen, Maschinenbau,
Richtung Metallurgie zu studieren“, berichtet der
25-jährige. „Der Inhalt hat mich sehr interessiert, als
Studium war es mir aber zu theoretisch. Ich freue mich
sehr, bei thyssenkrupp Steel diese Ausbildung machen zu
können. Von meiner Familie weiß ich, thyssenkrupp ist ein
verlässlicher Arbeitgeber – und die Ausbilder und meine
neuen Kollegen sind echt nett.“
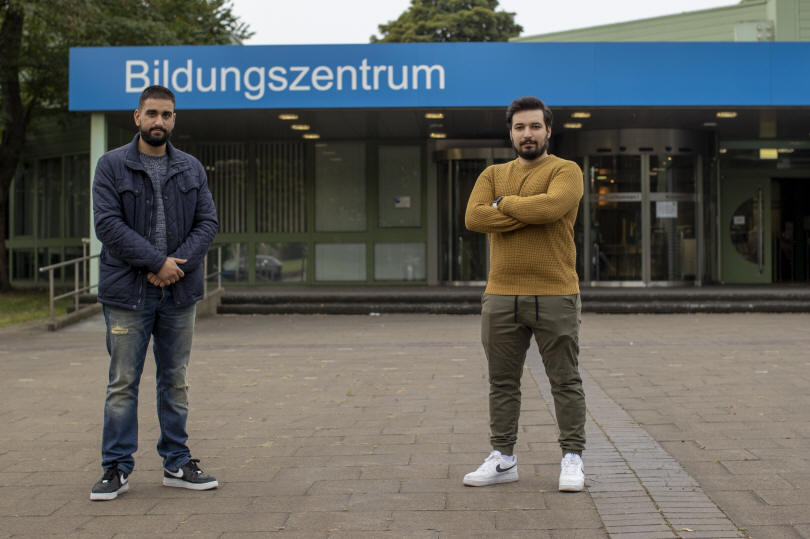
Zwei neue Kollegen: Oguzhan Öncü und Yusuf Akdogan sind
zwei der 300 Auszubildenden, die jetzt in einem der 22
Ausbildungsberufe bei thyssenkrupp Steel starten.
Der
Zusammenhalt und die Stimmung im Team sind auch für Yusuf
Akdogan wichtig. Der Auszubildende zum Elektroniker für
Maschinen- und Antriebstechnik in Duisburg hat während
seiner ersten Ausbildung nach dem Abitur gemerkt, dass er
sich eigentlich für Elektronik interessiert. Heute ist
der 21-jährige froh, dass der Wechsel in die Ausbildung
bei thyssenkrupp Steel so gut geklappt hat. „Wir sind ein
kleines Team von drei Leuten und ich freue mich darauf,
die neuen Kollegen besser kennenzulernen“, sagt Akdogan.
Auch sein Ausbilder sei für ihn ein klasse Typ: „Er hat
uns schon sehr viel gezeigt, sowohl im Bildungsbereich
als auch auf dem Werkgelände. Wenn wir in sechs Monaten
in die Betriebe gehen, wissen wir schon ein bisschen, wie
das abläuft.“
Die beiden Duisburger schauen auf ihren Einstieg in das
Ausbildungsteam und in die Praxis zufrieden zurück. „So
habe ich mir das vorgestellt“, so Öncü. „Wir haben direkt
eine Sicherheitsunterweisung erhalten. Wenn man neu ist,
muss man schließlich wissen, worauf man achten muss.“
Besonders freut sich Akdogan darüber, dass sich die
Ausbildung zeitlich mit seinem neuen Hobby vereinbaren
lässt; vor einem Jahr habe er angefangen, Tennis zu
spielen und freue sich darüber, langsam immer besser zu
werden. „Ich freue mich darüber, dass es mit der
Ausbildung nun losgeht und ich trotzdem weiterhin Zeit
für mein Hobby habe.“
Insgesamt starten in Duisburg 193 Auszubildende, in
Bochum 35 an der Essener Straße und 14 an der Castroper
Straße. Am Standort Dortmund fangen 31 Auszubildende an,
in Finnentrop insgesamt sechs und in Kreuztal-Eichen 21.
Abschluss in besonderen Zeiten Die Auszubildenden der
Abschlussprüfung im Sommer haben ihre Ausbildung in den
vergangenen Monaten unter außergewöhnlichen Umständen
erfolgreich beendet.
„Ausbildung im Home Schooling hat es bei uns so in dem
Ausmaß auch noch nicht gegeben,“ zieht Grigo Bilanz. Von
jetzt auf gleich sei durch den so genannten Lock-down im
März die Ausbildung auf „Heimarbeit“ umgestellt worden,
wobei thyssenkrupp Steel durch die
Digitalisierungsinitiativen in der Erstausbildung bereits
relativ gut vorbereitet war. Sowohl die Auszubildenden
als auch die Ausbilder haben die Herausforderung
angenommen und sich auf die neue Situation eingelassen.
„Die Ausbildung des letzten halben Jahres hat von uns
allen höchste Disziplin und besonderes Engagement
erfordert. Der Zusammenhalt in den Ausbildungsteams hat
mich sehr beeindruckt. Aber ganz ehrlich: die
eigentlichen „CoronaJahrgänge“ kommen jetzt erst noch,
die Herausforderungen für uns als Ausbildungsbetrieb, für
die allgemeinbildenden Schulen und für die Berufsschulen
werden uns noch mindestens für die nächsten zwei bis drei
Jahre begleiten.“
Von den 174 Abschlusskandidaten haben 150 ihre Ausbildung
erfolgreich beendet, 56 von ihnen mit gutem oder sehr
gutem Ergebnis. 93 der Absolventen hat thyssenkrupp Steel
unbefristet übernommen.
|
Elektro-Roheisen aus Hochofen 2.0:
thyssenkrupp stellt Bundeswirtschaftsminister Altmaier
und Ministerpräsident Laschet innovatives Konzept zur
grünen Transformation der Stahlhütte Duisburg vor
|
Duisburg, 28. August 2020 - Die grüne
Transformation von Deutschlands größtem Stahlhersteller
nimmt weiter Form an. thyssenkrupp Vorstandschefin
Martina Merz überreichte heute das Konzept zum Bau einer
ersten Direktreduktionsanlage mit einem integrierten
Schmelzaggregat (Hochofen 2.0) am Standort Duisburg an
Bundeswirtschaftsminister Peter Altmaier und
NRW-Ministerpräsident Armin Laschet.
Bundeswirtschaftsminister Peter Altmaier: „thyssenkrupp
setzt heute ein starkes Signal für ambitionierten
industriellen Klimaschutz. Stahl ist eine deutsche
Schlüsselindustrie. Wir müssen alles tun, damit in
Zukunft klimafreundlicher und wettbewerbsfähiger grüner
Stahl aus Deutschland kommt. Wir haben mit dem
Handlungskonzept Stahl die Rahmenbedingungen definiert.
Jetzt kommt es auf die Umsetzung und konkrete Projekte
an. Die hier geplante integrierte Direktreduktionsanlage
ist dafür ein exzellentes Beispiel.“
Nordrhein-Westfalens Ministerpräsident Armin Laschet:
„Nordrhein-Westfalen ist mit seiner einzigartig dichten
und vernetzten Unternehmens- und Forschungslandschaft ein
idealer Standort, um voranzugehen und Vorbild für ein
europäisches Zentrum für den Aufbau klimaneutraler
Industrien zu werden. Das zeigt sich auch an diesem
richtungsweisenden Projekt am Stahlstandort Duisburg:
thyssenkrupp hat damit die Chance, erneut
Industriegeschichte zu schreiben, wenn das Unternehmen
bei der Transformation zur klimaneutralen Industrie und
der Entwicklung von grünem Stahl entschlossen vorangeht.
Wir als Politik werden die Branche dabei unterstützen.
Hier sind alle gefordert: Bund und Land aber auch die
Europäische Union.“
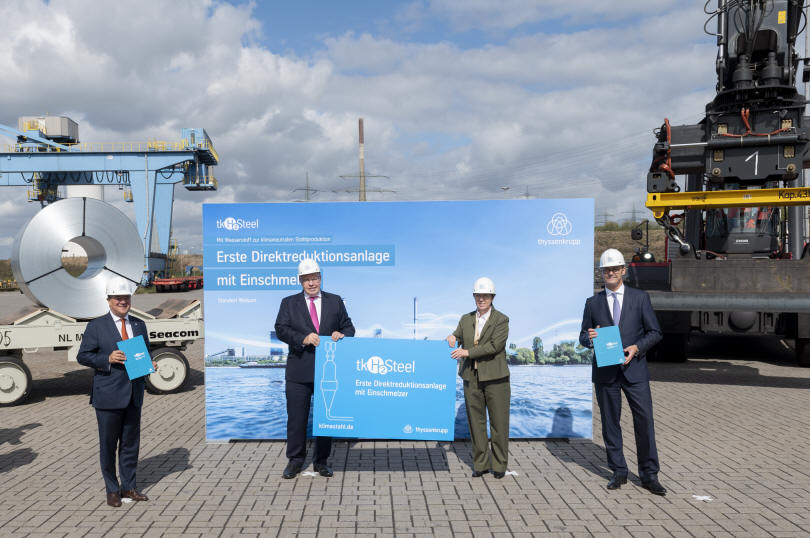
NRW-Ministerpräsident Armin Laschet (von links) und
Wirtschaftsminister Peter Altmaier bei thyssenkrupp in
Duisburg: thyssenkrupp Chefin Martina Merz überreicht das
Konzept zum Bau einer ersten Direktreduktionsanlage mit
einem integrierten Schmelzaggregat (Hochofen 2.0) am
Standort Duisburg – rechts Stahlchef Bernhard Osbur
Das zurzeit einzige Konzept dieser Art bringt eine Reihe
von Vorteilen mit sich. Es setzt weitgehend auf den
bestehenden Strukturen von Europas größtem integrierten
Stahlstandort auf und kommt dadurch mit deutlich
geringeren Investitions- und Betriebskosten aus. Ein
weiteres entscheidendes Plus und großer Vorteil für die
Kunden ist die Beibehaltung des kompletten
Produktportfolios, weil die bestehenden Stahlwerke und
Prozesse weiter genutzt werden können. Möglich wird
dieser effiziente Weg zur Klimaneutralität durch eine
Innovation: Das in der Direktreduktionsanlage erzeugte
feste Material wird mit einem integrierten
Schmelzaggregat verflüssigt.
In diesem Hochofen 2.0 entsteht so ein
„Elektro-Roheisen“, das im bestehenden Hüttenverbund
energieeffizient weiterverarbeitet werden kann. Die
integrierte Direktreduktionsanlage soll künftig mit
grünem Wasserstoff und grünem Strom betrieben werden und
ist ein wesentlicher Schritt zur Erreichung der
Klimaziele des Unternehmens und des Pariser
Klimaschutzabkommens. thyssenkrupp hat sich zum Ziel
gesetzt, bis 2030 seine CO2- Emissionen um 30 Prozent zu
reduzieren. thyssenkrupp plant, den Hauptteil der Anlage
bis 2025 fertigzustellen und dann bereits 400.000 Tonnen
grünen Stahl zu produzieren. Für 2030 sind bereits 3
Millionen Tonnen klimaneutraler Stahl vorgesehen.
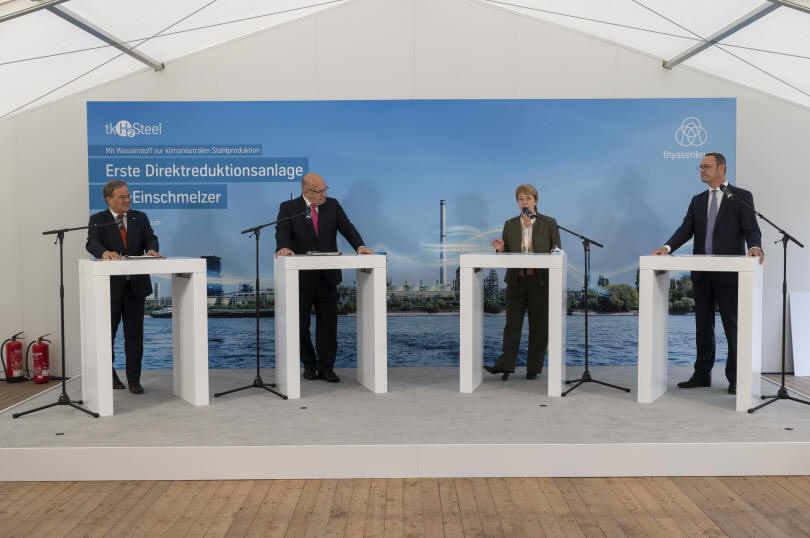
Auf dem Weg zum grünen Stahl:
NRW-Ministerpräsident Armin Laschet und
Bundeswirtschaftsminister Peter Altmaier zu Besuch bei
thyssenkrupp Steel in Duisburg. thyssenkrupp CEO Martina
Merz und Stahlchef Bernhard Osburg präsentieren das
Konzept für eine erste integrierte Direktreduktionsanlage
am Standort Duisburg. Von links nach rechts.
Enormes Potenzial der Stahlindustrie für
effektiven Klimaschutz
Der Stahlstandort Duisburg steht heute für rund zwei
Prozent der CO2-Emissionen in Deutschland. Entsprechend
groß ist auch das CO2-Senkungspotenzial, wenn es gelingt,
diese Emissionen in Zukunft gegen Null zu führen.
thyssenkrupp setzt dabei vor allem auf
Wasserstoff:
Gegenwärtig laufen Tests, um Wasserstoff im
konventionellen Hochofenbetrieb einzusetzen. Ziel ist,
kurzfristig den CO2-Footprint der Stahlproduktion zu
senken und erste Mengen CO2- neutralen Stahls zu
produzieren. Der nächste Meilenstein wird dann der Bau
der neuartigen, integrierten Direktreduktionsanlagen
sein, durch die die Emissionen entscheidend gesenkt
werden können.
thyssenkrupp Vorstandsvorsitzende Martina Merz: „Unsere
Expertinnen und Experten im Stahl haben ein technologisch
anspruchsvolles, integriertes Klimakonzept für den
größten Stahlstandort in Europa vorgestellt. Aufbauend
auf diesem Konzept werden wir im Rahmen einer
Umsetzungsstudie bis Anfang 2021 die Details für den
nachhaltigen Umbau unserer Produktion festlegen. Das
Konzept wird eine Signalwirkung weit über Duisburg hinaus
entfalten. Wir sind uns mit der Politik einig, dass kein
Unternehmen die Transformation alleine stemmen kann. Es
braucht anfangs geeignete Förder- und Anreizinstrumente.“
Stärkung der
Wettbewerbsfähigkeit und starkes Signal für Duisburg und
NRW
Ein weiterer Vorteil des Konzepts ist die Stärkung des
Standortes in Duisburg. In der Region Rhein-Ruhr sind die
Voraussetzungen gegeben, entlang der Wertschöpfungskette
Stahl die Transformation effizient und zukunftssicher
umzusetzen. Ein wesentlicher Vorteil des heute
vorgestellten Konzepts ist zudem der vergleichsweise
schnelle Hochlauf einer klimaneutralen Stahlproduktion.
Die erste Direktreduktionsanlage mit Einschmelzaggregat
wird eine Jahreskapazität von 1,2 Millionen Tonnen haben.
Wenn zunächst noch nicht genug grüner Wasserstoff zur
Verfügung steht, kann die Anlage mit Erdgas betrieben
werden. Bereits dann werden die CO2-Emissionen erheblich
gesenkt und zugleich signifikante Mengen an grünem Stahl
produziert werden – ohne Abstriche bei der Qualität der
Produkte. „Wir können im integrierten Hüttenverbund
unseren geplanten Hochofen 2.0 kostengünstiger betreiben
als auf der grünen Wiese.
Das ist einer der vielen Vorteile des Standortes
Duisburg“, erläutert Bernhard Osburg, Sprecher des
Vorstands von thyssenkrupp Steel. „Wir wollen unseren
Kunden über diese grüne Produktionsroute CO2-freien Stahl
zur Verfügung stellen – in den gewohnten Güten und über
das gesamte Produktspektrum. thyssenkrupp Steel kann den
Kern für eine grüne Industriewende in der
Rhein-Ruhr-Region bilden, weil wir Ausgangspunkt für
zahlreiche Wertschöpfungsketten sind. Dieses Ökosystem
wollen wir nutzen. Wir sind startklar.“
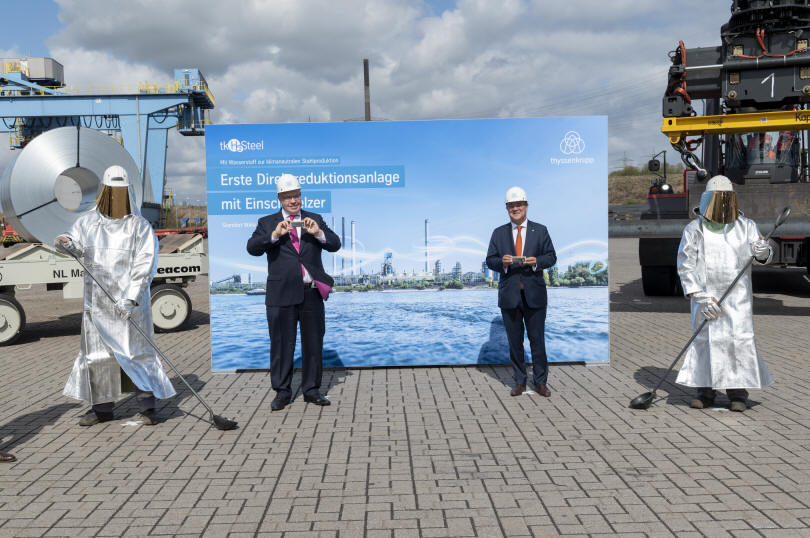
Bundeswirtschaftsminister Peter Altmaier und
NRW-Ministerpräsident Armin Laschet bei thyssenkrupp in
Duisburg 2. von links: Bundeswirtschaftsminister Peter
Altmaier daneben NRW-Ministerpräsident Armin Laschet, und
die Schmelzer Bünyamin Colakdemirci und Daniel Garske
|
Digitalisierte Logistik: thyssenkrupp Steel testet App
zum Tracking von Schubleichtern |
Duisburg, 23. Juni 2020 - Rund 240
Kilometer sind es mit dem Schiff über den Rhein vom
Europoort Rotterdam bis zum Hüttenwerk von thyssenkrupp
Steel in Duisburg. Die Wasserachse spielt bei der
Rohstoffversorgung des Werks eine wichtige Rolle und der
direkte Weg ist ein entscheidender Standortvorteil: Bis
zu 10.000 „Schubleichter“ beliefern den Werkhafen jedes
Jahr mit Eisenerz, Kohle sowie weiteren benötigten
Rohstoffen. Dabei handelt es sich um schwimmende
Container, die mit ihren mehr als 75 Metern Länge jeweils
bis zu 2.700 Tonnen Rohstoffe transportieren können.
Ein Verkehrsaufkommen, das gut koordiniert sein will,
denn der Platz in den eigenen Häfen Walsum und Schwelgern
ist endlich: nur eine begrenzte Zahl von Leichtern kann
gleichzeitig geparkt oder gelöscht werden. Im Rahmen der
Digitalisierungsstrategie in der Logistik optimiert
thyssenkrupp Steel die Leichterkoordination nun mit
moderner Sensortechnologie.
Der Schlüssel zum Erfolg: Informationsaustausch Die
Logistik ist hin und wieder nur mit kurzem Vorlauf
planbar: Unwetter oder schlechte Sicht durch Nebel können
genauso zu Verzögerungen führen wie ein niedriger
Rheinpegel. Auch Wartungen an den Hochöfen senken
vorübergehend den Materialbedarf.
Die Folge: kurzfristige Änderungen im Leichterverkehr.
„Es gibt Störfaktoren, die wir beachten müssen“,
verdeutlicht Christoph Pohl von der Umschlag- und
Lagerlogistik und zuständig für den Rohstoffumschlag in
den Werkhäfen.
„Die lassen sich alle meistern – aber damit das gelingt,
müssen wir vor allem die notwendigen Informationen
flexibel und schnell austauschen.“ Komplex wird es dabei,
weil viele Gewerke beteiligt sind und über Änderungen
informiert werden müssen: von der Hafendisposition bis
zum Hochofen, von den Schiffern bis zu den Kranführern in
den Werkhäfen, von Rotterdam bis Duisburg. Damit es
reibungslos läuft, muss viel kommuniziert werden.
„Unser Ziel war daher eine smarte
digitale Lösung, mit der alle Prozesspartner Zugriff auf
ein Live-Abbild der Lieferkette erhalten“, erklärt Walter
Scheider von der thyssenkrupp Steel Umschlag- und
Lagerlogistik. „Das reduziert den Abstimmungsaufwand und
ermöglicht es, die Prozesse besser zu koordinieren.“
Stets alles im Blick Die
wichtigsten Arbeitsgeräte, um die mehr als 100 Leichter
und diverse Schubboote entlang des Rheins sowie in den
Häfen zu koordinieren: eine Menge Betriebsdaten, Kameras
und viele Telefone. Das wollten die Logistiker
vereinfachen und suchten gemeinsam mit der IT, der
Umschlag- und Lagerlogistik sowie der
Rohstoffkoordination nach einer Lösung, wie alle
Beteiligten stets den Überblick behalten.
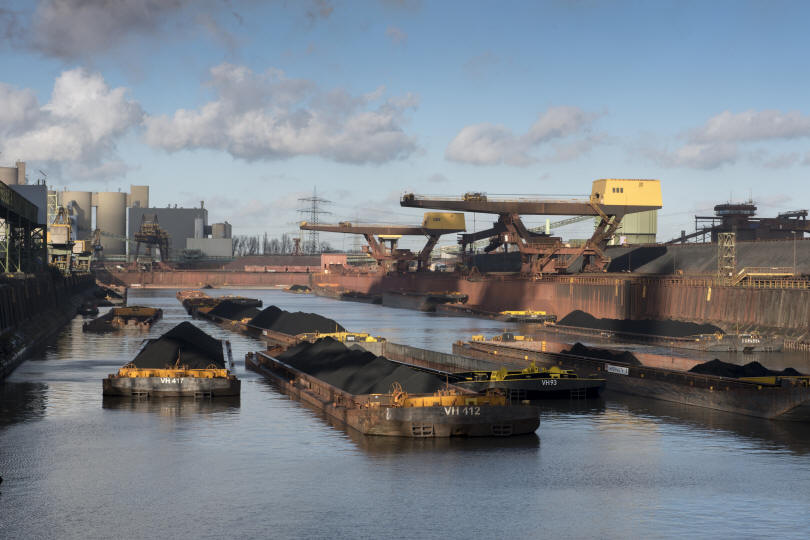
Schubleichter im Werkhafen Schwelgern in Duisburg.
In der Folge ist nun jeder Leichter IoT-fähig („Internet
of things“) und mit einem solarbetriebenen GPS-Sensor
ausgestattet. Die GPSDaten werden mit Informationen zu
den jeweiligen Aufträgen und Ladungen zusammengeführt.
Das Ergebnis ist eine digitale Landkarte, auf der alle
Beteiligten jeden einzelnen Leichter zu jeder Zeit im
Blick behalten können – inklusive Informationen zur
Tonnage, dem geladenen Rohstoff und mittels künstlicher
Intelligenz berechneter Ankunftszeit im Zielhafen. In der
Folge können Zeit und Kosten gespart werden – zum
Beispiel, indem Schiffsführer auf dem Weg nach Duisburg
ein Signal erhalten und einfach langsamer und
spritsparender fahren, wenn ohnehin absehbar ist, dass
sie sonst vor dem Werkhafen auf Einfahrt warten müssten.
„Durch die Live-Verfolgung können wir deutlich besser im
Voraus planen“, erklärt Christoph Pohl. „Gleichzeitig
helfen uns die gesammelten Daten bei der Auswertung und
Optimierung der Prozesse: Wir können etwa sehr genau
verfolgen, bei welchen Leichtern es wo und wann zu
Wartezeiten kommt und dann auf Spurensuche gehen, um
diese zu verringern.“
Digitale Innovation schnell umgesetzt
Aber wie kam man von der innovativen Idee zur fertigen
App? Hier wurde ein innovativer Ansatz gewählt: ein
interdisziplinäres Expertenteam erarbeitete innerhalb von
nur drei Wochen einen Prototyp der App, der in einem
Feldversuch mit sechs Schubleichtern getestet wurde.
Neben der technischen Machbarkeit ließen sich dabei
kurzerhand auch die Nutzbarkeit im laufenden Betrieb
beweisen und weitere Erkenntnisse sammeln. „Das neue
Arbeitsformat war die Basis dafür, dass wir die
innovative Idee des Trackings der Schubleichter in einem
experimentellen Umfeld ausprobieren und so schnell
Ergebnisse erzielen konnten“, so Tim Rupp vom Bereich
Digitale Innovation.
Gleichzeitig hat das Team noch eine für das Unternehmen
spezifische, cloud-basierte Plattform errichtet, auf
deren Grundlage sich künftige weitere
Tracking-Anwendungen umsetzen lassen. Die neue App
startet in diesen Tagen in eine Testphase mit Beteiligten
aus allen involvierten Bereichen. Ein erster Roll-Out in
der Breite ist für das kommende Geschäftsjahr geplant.
Weiterer Schritt auf dem Weg
zur digitalisierten Logistik
Das Tracking soll langfristig als Basis für weitere
Optimierungen und Automatisierungen dienen. Denkbar wären
etwa Auswertungen zum optimalen Hafenfüllgrad, die
Integration von prognostizierten Wasserstandsdaten oder
das Einbeziehen externer Schiffe, um anfallende
Liegegebühren zu reduzieren. Das Tracking der Leichter
ist dabei ein weiteres Puzzlestück auf dem Weg zur
digitalisierten Logistik, die thyssenkrupp Steel im
Rahmen der Digitalisierungsstrategie verfolgt.
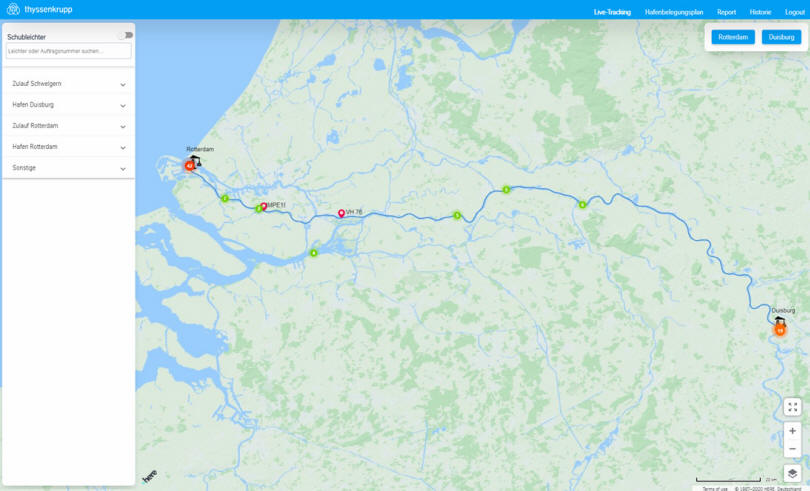
Tracking - In der App werden
die Schubleichter auf einer digitalen Karte angezeigt.
Das Kartenmaterial liefert das Unternehmen HERE
Technologies.
|
Innovationspreis Reallabore – Liefer-Drohne „Stahlbiene“
setzt sich gegen zahlreiche Mitbewerber durch
|
Berlin/Kassel/Duisburg, 27. Mai 2020 -
Das gemeinsame Projekt delivAIRy von doks. innovation
GmbH und thyssenkrupp Steel Europe AG gewinnt den
Innovationspreis Reallabore des
Bundeswirtschaftsministeriums in der Kategorie
‚Einblicke‘.
Den Preis verlieh die fünfköpfige Experten-Jury rund um
Thomas Jarzombek, dem Beauftragten der Bundesregierung
für Digitale Wirtschaft und Start-ups, in einer
Online-Zeremonie.
Bei thyssenkrupp wird sie liebevoll „die Stahlbiene“
genannt: die Liefer-Drohne delivAIRy®. Regelmäßig macht
sie sich auf den Weg und liefert Proben über das
Werksgelände in Duisburg zur Weiterverarbeitung ins
Labor. Sie ist Teil des gemeinsamen Projektes des
Kasseler Start-Ups doks. innovation GmbH und Deutschlands
größtem Stahlhersteller thyssenkrupp Steel zur Erprobung
von drohnengestützten Lieferprozessen auf dem
Werksgelände. Für das zukunftsweisende, derzeit noch
laufende Projekt wurden die beiden Partner nun mit dem
Innovationspreis Reallabore des
Bundeswirtschaftsministeriums ausgezeichnet.
„thyssenkrupp bietet einen Anwendungsfall fern ab von
last-mile-delivery, der bereits heute umsetzbar ist“,
weiß Benjamin Federmann, Gründer und Geschäftsführer von
doks. innovation GmbH, „durch die gute Zusammenarbeit mit
thyssenkrupp und den lokalen Behörden können wir
zukunftsweisende Technologien bereits heute unter realen
Bedingungen erproben und etablieren“.
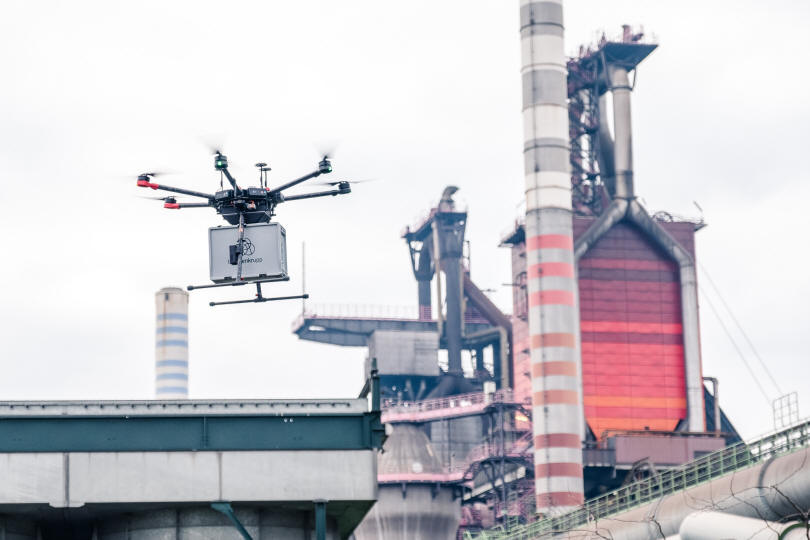
Von doks. innovation und thyssenkrupp Steel gemeinsam
entwickelt: Die Drohne, Stahlbiene genannt, liefert
automatisiert – ohne das Zutun eines Piloten – Proben
über das Duisburger Werksgelände von thyssenkrupp und
überfliegt hierbei unter anderem Bundesstraßen und
Bahnschienen. Sie verfügt über modernste
Sicherheitsstandards und kann im Notfall einen speziell
ausgewiesenen Notlandplatz anfliegen.
„Die Transportdrohne, die zuverlässig und automatisiert
über unser Werkgelände fliegt, ist ein konkretes und
sichtbares Beispiel für Digitalisierung im
Industrie-Alltag. Dieses Projekt macht den Transport
nicht nur modern und digital, sondern auch nachhaltig,
effizienter und sicherer“, erläutert Bernhard Osburg,
Sprecher des Vorstands der thyssenkrupp Steel Europe AG.
„Den Preisträgern des Innovationspreises Reallabore
gelingt es auf vorbildliche Weise, digitale Technologien
wie künstliche Intelligenz oder Blockchain im Reallabor
in die konkrete Anwendung zu bringen und damit Mehrwert
vor Ort zu schaffen.
Damit machen sie gleichzeitig anderen Unternehmen,
Verwaltungen und Forschungseinrichtungen Mut, eigene
Innovationsprojekte umzusetzen. Doch auch die Politik ist
gefragt: Viele Beiträge zeigen deutlich, wo neue
Freiräume notwendig sind, um Erprobungsprojekte möglich
zu machen“, so Bundeswirtschaftsminister Altmaier.
„Wenn sich der automatisierte Flugroboter jetzt beim
Laborprobentransport bewährt, könnte er in Zukunft auch
in anderen Bereichen der internen Logistik zum Einsatz
kommen“, blickt Projektleiter Dr. Thomas Lostak,
Teamleiter im Innovationsbereich von thyssenkrupp Steel
optimistisch in die Zukunft. „Die Drohne lässt sich
individuell per App anfordern. Die Auslieferung
zeitkritischer Sendungen auf unserem Duisburger
Werksgelände können wir damit voll automatisieren und
digitalisieren“, so Lostak weiter. Außerdem komme das
Projekt sehr gut bei den Kolleginnen und Kollegen an. Die
abstrakte Thematik der Digitalisierung werde durch den
Drohneneinsatz eindrucksvoll greifbar. Das liefere
frischen Rückenwind für weitere Digitalisierungsprojekte.
Im Reallabor in Duisburg erproben doks. innovation und
thyssenkrupp, was im Allgemeinen als die Zukunft gilt:
Die Drohne liefert automatisiert (ohne das Zutun eines
Piloten) Proben über das gesamte Werksgelände und
überfliegt hierbei unter anderem Bundesstraßen und
Bahnschienen. Sobald die Transportbox mit einem
patentierten Greifmechanismus an der Drohne befestigt
ist, kann sie per Knopfdruck an ihren Zielort geschickt
werden.
Im Gegensatz zu dem normalerweise eingesetzten Auto,
benötigt die Drohne nur 10 Minuten bis zu ihrem Zielort
und spart so nicht nur Zeit, sondern schont auch die
Umwelt. Außerdem verfügt die Drohne über modernste
Sicherheitsstandards und kann im Notfall einen speziell
ausgewiesenen Notlandplatz anfliegen. doks. innovation
GmbH Das Start-Up doks. innovation wurde 2017 im Umfeld
des Fraunhofer Instituts für Materialfluss und Logistik
IML in Dortmund gegründet. Seit 2018 am Hauptsitz in
Kassel tätig, entwickelt das Unternehmen Lösungen zur
automatisierten Datenerfassung und - verarbeitung in der
Logistik.
Hierzu werden innovative Trägertechnologien, beispielsweise Drohnen,
hochsensible Sensoren und intelligente Software mit
Machine Learning-Algorithmen zu einem leistungsstarken
Ökosystem für effiziente Logistikabläufe kombiniert.
thyssenkrupp Steel Europe AG Die Stahlsparte von
thyssenkrupp gehört zu den weltweit führenden Anbietern
von Qualitätsflachstahl.
Mit rund 28.000 Mitarbeitern liefert das Unternehmen
hochwertige Stahlprodukte für innovative und
anspruchsvolle Anwendungen in verschiedensten
Industriezweigen, darunter die Automobilindustrie, der
Maschinenbau, der Sonderfahrzeugbau, die Haushaltsgeräte-
und Verpackungsindustrie, der Energiesektor und die
Baubranche. Kundenspezifische Werkstofflösungen und
Dienstleistungen rund um den Werkstoff Stahl
komplettieren das Leistungsspektrum.
thyssenkrupp Steel erfüllt dabei die steigenden
Anforderungen an immer effizientere Leichtbau- und
Sicherheitsstandards, erforscht und entwickelt neue
Hightech-Stähle und setzt Maßstäbe bei Oberflächen- und
Verarbeitungstechnologien. Unsere intensive Forschungs-
und Entwicklungsarbeit sichert die Grundlage für unseren
nachhaltigen Erfolg. Mit einem Produktionsvolumen von
jährlich ungefähr 12 Millionen Tonnen Rohstahl ist
thyssenkrupp Steel der größte Flachstahlhersteller in
Deutschland.
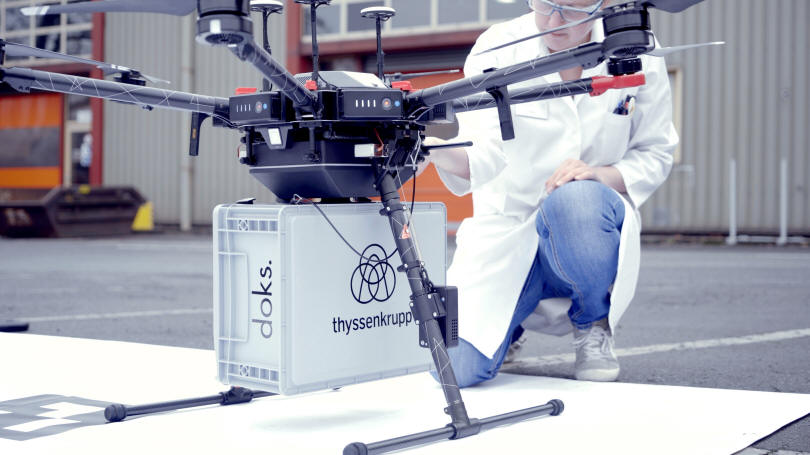
Spart Zeit und schont die
Umwelt: Sobald die Transportbox mit einem patentierten
Greifmechanismus an der Drohne befestigt ist, kann sie
per Knopfdruck an ihren Zielort geschickt werden. Im
Gegensatz zu dem normalerweise eingesetzten Auto,
benötigt die Drohne nur 10 Minuten bis zu ihrem Zielort
und spart so nicht nur Zeit, sondern schont auch die
Umwelt.
|
60 Jahre Betriebsvereinbarung: Arbeitssicherheit hat
trotz Corona höchste Priorität bei thyssenkrupp Steel
|
Duisburg, 28. März 2020 - Das
Corona-Virus bestimmt derzeit das Arbeitsleben. Viele
Mitarbeitende befinden sich im Home-Office, doch nicht
für alle ist das möglich. All jene Mitarbeitende, die
beispielsweise die Produktion aufrechthalten, kommen
weiterhin täglich an ihren gewohnten Arbeitsplatz und
müssen sich dort an die Hygienevorschriften halten.
„Das Corona-Virus beeinflusst unseren Alltag auf bisher
ungekannte Weise. Doch auch, wenn die neuen
Hygienemaßnahmen unsere Aufmerksamkeit fordern und
zwingend umgesetzt werden müssen, hat nach wie vor die
Arbeitssicherheit höchste Priorität“, sagt Markus Grolms,
Arbeitsdirektor und Personalvorstand bei thyssenkrupp
Steel. Denn Arbeitssicherheit hat eine lange Tradition
bei thyssenkrupp Steel.
Vor nunmehr 60 Jahren schlossen Vorstand und Betriebsrat
der August Thyssen-Hütte AG eine Betriebsvereinbarung,
durch die allen Belegschaftsmitgliedern in der Produktion
das Tragen von Sicherheitsschuhen zur Pflicht gemacht
wurde. Bis dahin trugen die Hochöfner lediglich
Holzschuhe. Und auch sonst hat sich hinsichtlich der
Arbeitssicherheit bei thyssenkrupp Steel einiges getan.
Aus Holzschuhen werden Sicherheitsschuhe Die Holzschuhe
am Hochofen gab es bereits seit den 1920er Jahren. Doch
wirklich sicher war das nicht – die Anzahl an
Fußverletzungen war hoch.
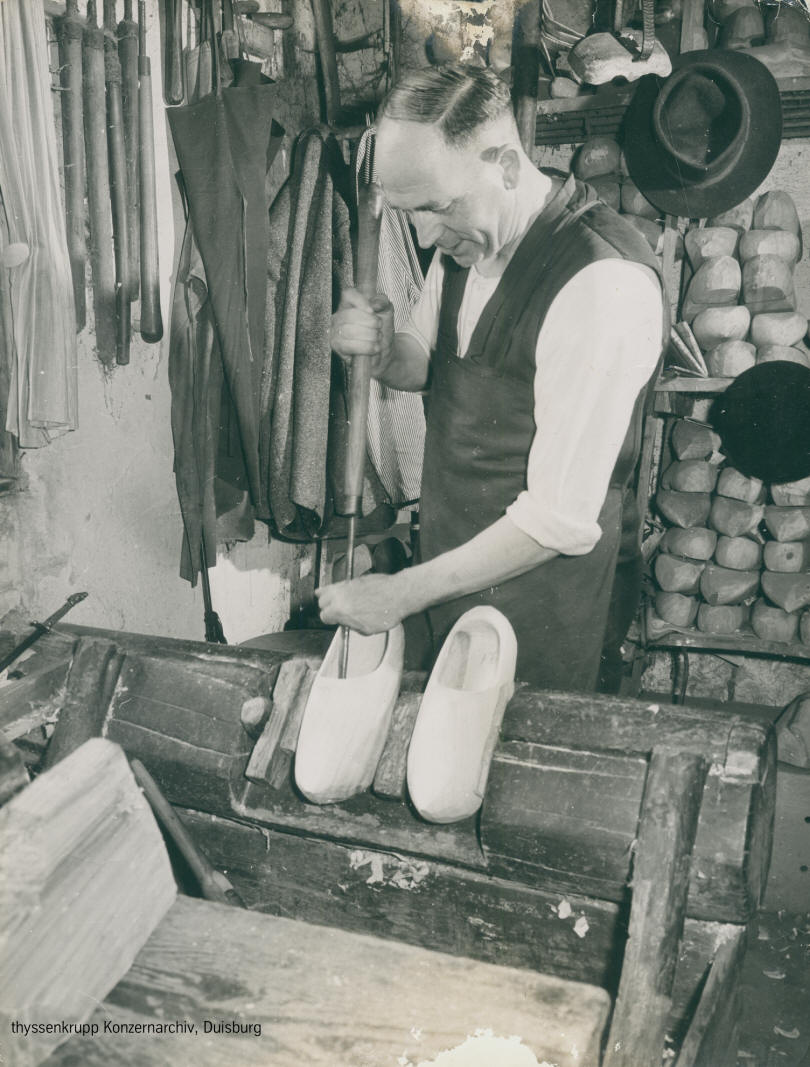
Bis in die 1920er Jahre arbeiteten die Hochöfner in
Holzschuhen, trotz enormer Verletzungsgefahr. Am 19.
April 1960 schloss das Unternehmen schließlich eine
Betriebsvereinbarung, die das Tragen von
Arbeitssicherheitsschuhen überall in der Produktion zur
Pflicht machte. Foto: thyssenkrupp Konzernarchiv,
Duisburg
Das Unternehmen handelte schließlich und machte das
Tragen von Sicherheitsschuhen mit der
Betriebsvereinbarung vom 19. April 1960 überall in der
Produktion zur Pflicht. Anfangs hieß es von den
Mitarbeitenden noch, die neuen Sicherheitsschuhe seien
schwer, unbequem und man könne außerdem Holzschuhe viel
schneller vom Fuß bekommen als einen Sicherheitsschuh,
sollte man in heißes Eisen treten.
Nach
und nach etablierten sie sich jedoch zu einem der
wichtigsten Utensilien hinsichtlich der
Arbeitssicherheit. In ihrer modernen Form sind die
Stahlkappensicherheitsschuhe – neben Helm, Spritzschutz
und Silbermantel – auch heute noch Pflicht, nicht nur am
Hochofen. Foto: thyssenkrupp Konzernarchiv, Duisburg
Auch wenn die neuen Sicherheitsschuhe anfangs ungewohnt
für die Mitarbeitenden waren, reduzierte sich doch die
Zahl der Fußverletzungen drastisch. Sie etablierten sich
zu einem der wichtigsten Utensilien in der
Arbeitssicherheit und sind in ihrer modernen Form als
Stahlkappensicherheitsschuhe auch heute noch Pflicht.
Ziel: Eine Kultur der Arbeitssicherheit „Erst sicher und
dann gut“ – das ist heute das Motto des
Sicherheitskulturprogramms, das auf vielen Wegen und
Wänden bei thyssenkrupp Steel steht, seit das Programm
2018 ins Leben gerufen wurde. Denn der Schutz der
Gesundheit aller Mitarbeitenden ist der höchste Wert des
Unternehmens und auf lange Sicht ist es das Ziel, die
Arbeitssicherheit nicht nur technisch und organisatorisch
weiterzuentwickeln, sondern eine Kultur der Sicherheit
als obersten Wert zu leben.
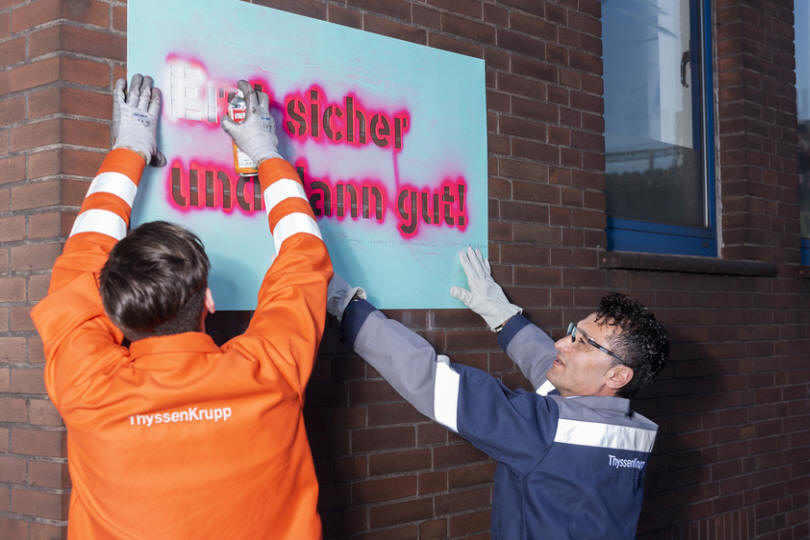
„Erst sicher und dann gut“ – dieses
Motto steht auf vielen Wegen und Wänden bei thyssenkrupp
Steel. Es gehört zum Sicherheitskulturprogramm, das 2018
ins Leben gerufen wurde. Die Mitarbeitenden werden aktiv
in Weiterentwicklungsmaßnahmen der Sicherheitskultur
einbezogen. Quelle: thyssenkrupp Steel
„Seit vielen Jahren sensibilisieren wir Führungskräfte
und Mitarbeitende dafür, wie wichtig ihre Sicherheit und
Gesundheit sind, mittels unterschiedlicher Schulungen und
Kampagnen – und wir stellen einen deutlichen Fortschritt
im Umgang mit der Arbeitssicherheit fest“, sagt Beatrice
Schenuit, leitende Sicherheitsingenieurin bei
thyssenkrupp Steel.
„Offen kommunizieren zu können und eine Kultur, in der
man aus Fehlern lernen kann, sind unerlässlich für eine
funktionierende Sicherheitskultur.“ Deshalb werden die
Mitarbeitenden aktiv in die Weiterentwicklung der
Sicherheitskultur einbezogen: Ideen werden zusätzlich auf
den Prüfstand gestellt, indem jede Maßnahme zunächst auf
ihre Praxistauglichkeit getestet und erst nach dem
MitarbeiterFeedback umgesetzt wird.
|
Innovative Sauerstofftechnologie für
den Hochofenprozess: Sequenz-Impuls-Prozess mit
induzierten Stoßwellen (SIP)
|
• Neues Verfahren von thyssenkrupp
entwickelt
• Hochofen in Duisburg als weltweit erster ausgerüstet
• Beitrag zum Klimaschutz
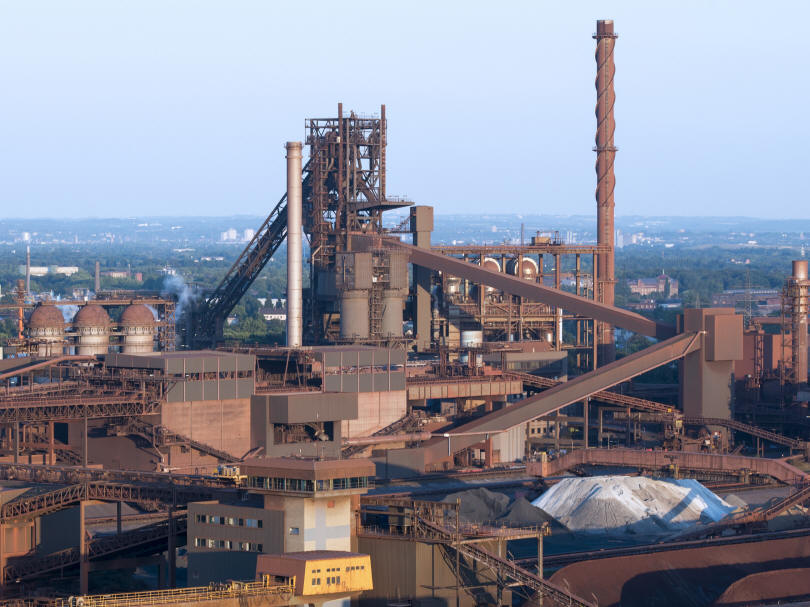
thyssenkrupp Steel Europe Hochofen Schwelgern1 - c
thyssenkrupp
Duisburg, 10. März 2020 - thyssenkrupp erprobt in
Duisburg mit dem „Sequenz-Impuls-Prozess mit induzierten
Stoßwellen“ eine neuartige Hochofentechnologie, um die
eigenen Prozesse effizienter zu gestalten. Zudem möchte
das Unternehmen mit der Technologie einen Beitrag zur
Minderung der CO2-Emissionen leisten – sowohl im eigenen
Unternehmen als auch weltweit durch die Vermarktung der
Technologie. Nach einem fundierten Forschungs- und
Entwicklungsprozess wurde nun auf der Zielgeraden die
weltweit erste Anlage am Hochofen Schwelgern 1 und somit
auch die Referenzanlage für die Vermarktung
fertiggestellt.
Neues Verfahren mit Potential
Das Resultat der von thyssenkrupp AT.PRO tec GmbH, einem
Unternehmen der thyssenkrupp Materials Trading GmbH, und
thyssenkrupp Steel Europe durchgeführten Entwicklungen
ist ein speziell auf den Hochofenprozess zugeschnittenes
innovatives Sauerstoffinjektionsverfahren.
„Die Verfahrensentwicklung wurde auf eine „Tiefenwirkung“
des Sauerstoffs ausgelegt. Ziel ist es dabei, die Gas-
und Flüssigkeitsströme des Hochofens zu verbessern und
somit eine Effizienzsteigerung zu erzielen. Grundlage
dafür sind die Kenntnis und die gezielte Anwendung
verschiedener gasdynamischer Phänomene bei der
Sauerstoffinjektion“, erläutert Dr. Rainer Klock, Manager
Ofenmetallurgie des Hochofenbetriebes Schwelgern von
thyssenkrupp Steel Europe, die neue Technologie.
Zur technischen Umsetzung wird in jede der 40 Blasformen
des Hochofens 1 eine zusätzliche Lanze eingesetzt durch
die der Sauerstoff injiziert wird. Jede der 40 Lanzen
wird von einer eigenen Injektionseinheit, der sogenannten
SIP-Box, versorgt.
„Ich freue mich, dass wir mit Schwelgern 1 einen der
größten Hochöfen Europas haben, an dem unsere
SIP-Technologie jetzt installiert ist“, sagt Gerd König,
geschäftsführender Gesellschafter der thyssenkrupp AT.PRO
tec GmbH. „In Kürze werden wir auch in der Lage sein,
durch Referenzwerte die Rentabilität der Technologie
nachzuweisen und aufzuzeigen, dass sie die Prozesse im
Hochofen optimiert.“
Die Ergebnisse der in
Zusammenarbeit mit der RWTH Aachen durchgeführten
Forschungen und Untersuchungen stimmen Jörg Glebe,
Geschäftsführer der thyssenkrupp AT.PRO tec GmbH,
zuversichtlich: „Bei einer Effizienzsteigerung des
Hochofenprozesses wird der Verbrauch der Reduktionsmittel
Koks und Einblaskohle optimiert. So können CO2-
Emissionen und Kosten reduziert werden. Schon ein
Austausch von fünf Kilogramm Koks durch Einblaskohle pro
Tonne Roheisen würde am Hochofen Schwelgern 1 zu einem
jährlichen Kosteneinsparpotential in Millionenhöhe
führen.“
Ausblick: Weltweite Vermarktung
Bereits jetzt stößt die Technologie auf breites
Interesse. Derzeit finden Gespräche mit großen
Anlagenbauern statt. Ziel ist es, das Verfahren
flächendeckend auf den Markt zu bringen und die
Ausrüstung von Hochöfen zu begleiten. „Wir sehen großes
wirtschaftliches Potential in unserer
Technologieentwicklung und sind überzeugt, dass sie sich
schnell auf dem Weltmarkt dursetzen wird“, sagt Wolfgang
Schnittker, CEO der thyssenkrupp Materials Trading.
Beitrag zur Klimastrategie der Stahlproduktion von
thyssenkrupp
Bis 2050 soll die Stahlproduktion bei thyssenkrupp
klimaneutral werden. In einem ersten Zwischenziel möchte
thyssenkrupp bis zum Jahr 2030 die Emissionen aus
Produktion und Prozessen im eigenen Unternehmen sowie die
Emissionen aus dem Bezug von Energie gegenüber dem
Referenzjahr 2018 um 30 Prozent senken. Die Vermeidung
von CO2 („Carbon Direct Avoidance“, CDA) ist dabei einer
von zwei Pfaden der Strategie.
In einem nächsten Schritt sollen dazu die Hochöfen
teilweise auf Wasserstoff umgestellt werden. Damit
schließlich alle Chancen zur weiteren Optimierung der
Hochofentechnologie ausgeschöpft werden, erprobt
thyssenkrupp die neue Sauerstoffinjektion den
„SequenzImpuls-Prozess mit induzierten Stoßwellen“ am
Großhochofen Schwelgern 1.
|
Der Stahlbereich von thyssenkrupp
richtet Regionalwettbewerb für „Jugend forscht“ in
Duisburg aus
|
84 Nachwuchstüftler stellen
ihre Ideen vor
Duisburg, 20. Februar 2020 - Da rauchen die Köpfe:
Naturwissenschaften und Mathematik sind die Bereiche, mit
denen sich junge Menschen im Rahmen von „Jugend forscht“
auseinandersetzen. Jahr für Jahr haben die
Teilnehmerinnen und Teilnehmer innovative Ideen für
verblüffende Lösungsansätze. 39 Projekte sind es in
diesem Jahr, die die Teilnehmenden bei Jugend forscht am
Mittwoch, 19. Februar 2020, im Technikzentrum von
thyssenkrupp in Duisburg einer Fachjury präsentiert
haben.
Die Stahlsparte ist bereits zum 38. Mal Gastgeber für die
Tüftlerwettbewerbe. Insgesamt haben in diesem Jahr 84
Schülerinnen und Schüler, Auszubildende und Studierende
aus dem Ruhrgebiet eigene wissenschaftliche
Fragestellungen in Kategorien wie Biologie, Chemie oder
Mathematik entwickelt, für die bisher keine Lösungen
existierten. Der Fantasie waren kaum Grenzen gesetzt, was
auch die ungebrochene Motivation zur Teilnahme
verdeutlicht.
Blindenpilot, überkochende Milch und Wärmebilddrohne
„Schaffst du“ lautet das diesjährige Motto des
Nachwuchswettbewerbs. In der Kategorie Technik haben Jens
Stuckenholz (17) und Konstantin Heimüller (17) vom
Andreas-Vesalius-Gymnasium in Wesel den ersten Platz
belegt. Sie haben einen Gurt erfunden, der sehbehinderten
Menschen mithilfe von Ultraschallsensoren und
Vibrationsmodulen mitteilt, wo und in welcher Entfernung
sich ein Hindernis befindet.
Auch bei „Schüler experimentieren“, der Juniorensparte
von „Jugend forscht“, gibt es einen ersten Platz. Dieser
ging an Tim Neidert (13) und Elisa Strom (12) vom
Immanuel-Kant-Gymnasium in Heiligenhaus in der Kategorie
Physik. Sie haben das Überkochverhalten verschiedener
Milcharten und verschiedene Tipps, die das Überkochen
verhindern sollen, untersucht. Zudem waren Auszubildende
von thyssenkrupp Steel unter den Gewinnern.
Ein dritter Platz in der Kategorie Arbeitswelt ging an
Linus Winstroth (20), David Todorovic (18) und Leon Luca
Koch (18) am Standort Duisburg. Ebenfalls ein dritter
Platz in der Kategorie Technik ging an Andrej Keiner
(19), Sami Hasan Kalay (20) und Lars Klimzak (19), die am
Standort Kreuztal eine Wärmebilddrohne entwickelt haben.
„‚Jugend forscht‘ bietet jungen Menschen eine wunderbare
Möglichkeit, über den Alltag hinauszudenken und aus einer
anfangs kleinen Idee einzigartige und praktikable
Lösungen zu entwickeln. Wenn Schülerinnen und Schüler,
Auszubildende und Studierende in ihrer Freizeit so viel
Energie und Freude in die Weiterentwicklung und
Erforschung einer Idee bis hin zum Prototypen
investieren, merke ich, wie viel Potenzial in unserem
Nachwuchs und damit in unserer Zukunft steckt“, sagt
Volker Grigo, Leiter der Ausbildung von thyssenkrupp
Steel.
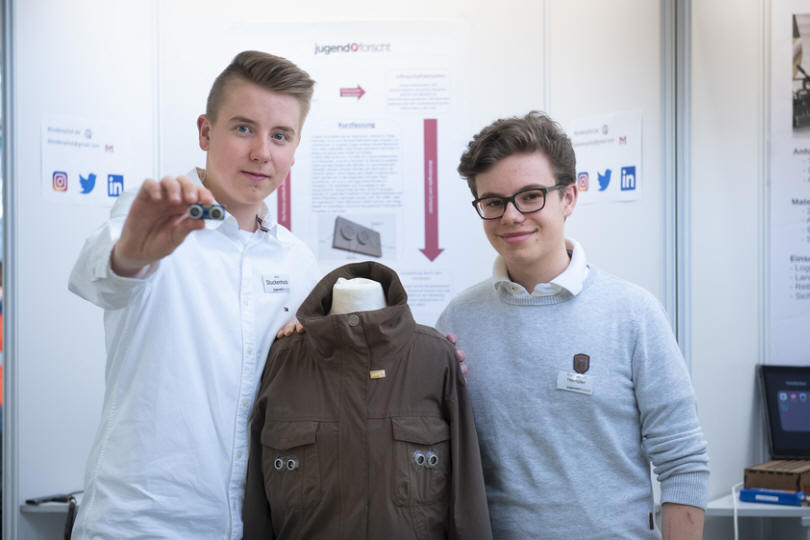
V. l.: Jens Stuckenholz (17) und Konstantin Heimüller
(17) vom Andreas-Vesalius-Gymnasium in Wesel haben den
ersten Preis in der Kategorie Technik belegt. Ihr
Blindenpilot hilft sehbehinderten Menschen dabei sich im
Alltag besser zurecht zu finden, indem
Ultraschallsensoren und Vibrationsmodule sie auf
Hindernisse hinweisen.
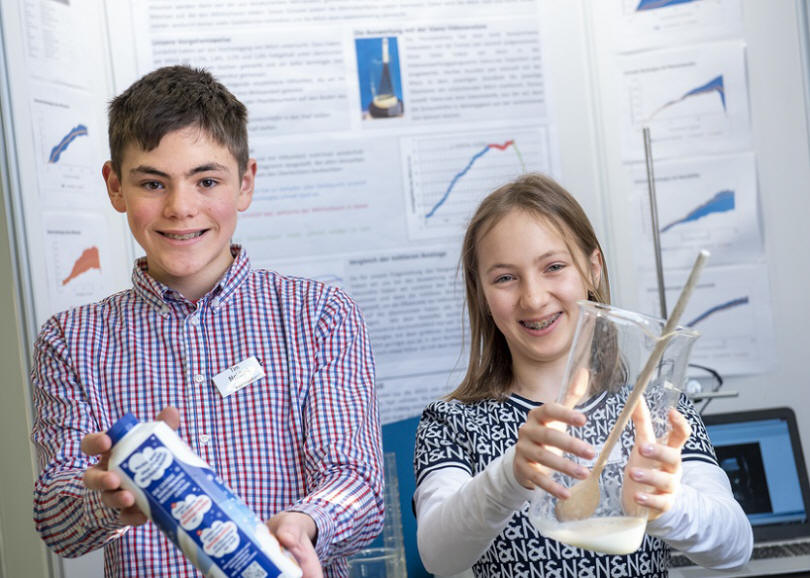
Warum kocht Milch im Topf über? Und welche Tipps dagegen
helfen wirklich? Tim Neidert (13) und Elisa Strom (12)
(v.l.n.r.) vom Immanuel-Kant-Gymnasium in Heiligenhaus
haben mit ihrem Experiment über die Eigenschaften von
kochender Milch den ersten Preis in der Kategorie Physik
bekommen.
Fotos: thyssenkrupp Steel
thyssenkrupp als Gastgeber des Regionalwettbewerbs
„Jugend forscht“
Neben vielen anderen Förderprogrammen, Kooperationen mit
Partner- und Hochschulen sowie Projekten für Schülerinnen
und Schüler engagiert sich thyssenkrupp seit 38 Jahren im
Rahmen des Wettbewerbs „Jugend forscht“ bzw. „Schüler
experimentieren“ für junge Menschen.
Am diesjährigen Regionalwettbewerb im Bildungszentrum
Duisburg nahmen 84 Kinder, Jugendliche und junge
Erwachsene aus Castrop-Rauxel, Duisburg, Düsseldorf,
Essen, Heiligenhaus, Kreuztal, Mülheim an der Ruhr,
Oberhausen, Sankt Augustin, Vreden und Wesel teil.
Die Siegerteams der regionalen Runde treten Anfang April
beim Landeswettbewerb in Leverkusen an. Abschließend geht
es ins Finale auf Bundesebene, deren Preisträger im Mai
2020 gekürt werden.
|
thyssenkrupp Steel digitalisiert
Auftragsdisposition im Eisenbahnbetrieb
|
Duisburg, 17. Februar 2020 - Rund 300
Kilometer Schienennetz erstrecken sich über das
Werksgelände von thyssenkrupp Steel im Duisburger Norden.
Die Eisenbahn ist der entscheidende Transportweg für
Rohstoffe und Produkte auf dem Gelände und über die
Werksgrenzen hinaus. Mit einer App vereinfacht
thyssenkrupp Steel seit Kurzem die Kommunikation zwischen
Auftragsdisponenten und Lokführern.
Altes System stieß an Grenzen
Bisher fand die Kommunikation vor allem über Sprechfunk
statt. Der Disponent erzeugte einen Auftrag im System,
informierte den Lokführer, wartete die Bestätigung des
Lokführers ab und bestätigte dann den Auftrag im System.
Ein aufwändiges und zeitraubendes Unterfangen für alle
Beteiligten. „Um das zu ändern, haben wir ein
interdisziplinäres Team gebildet“, erklärt Michael Heise,
Senior Engineer im Bereich Logistik bei thyssenkrupp
Steel. „Unser Ziel war ein digitaler Weg, der die
Erfassung von Arbeitsaufträgen ohne Kommunikation
zwischen Disponent und Lokführer ermöglicht.“
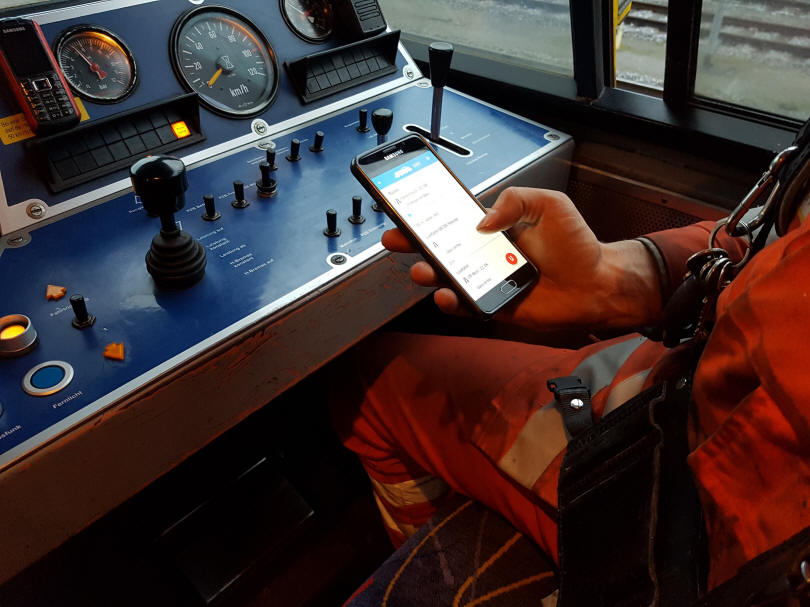
Nutzung der neuen Dispositions-App im Eisenbahnbetrieb
bei thyssenkrupp Steel.
Entwicklungsarbeit in Rekordzeit
Nach nur vier Wochen stand der Prototyp für den
Feldversuch bereit, inklusive eingebautem Feedback von
Lokführern und Disponenten. Die zugrundeliegende
cloud-basierte Systemarchitektur entwickelte das Team
dabei ebenfalls gleich mit. Das Ergebnis: Der Austausch
zwischen Disponent und Lokführer findet nun fast
ausschließlich über eine neu entwickelte App statt.
Insgesamt werden so eine Vielzahl von Gesprächen über
Sprechfunk überflüssig. Zudem können zukünftige Apps die
neue Cloud-Umgebung ebenfalls nutzen. Auch deswegen
zählte das Team um Michael Heise im Dezember 2019 beim
unternehmensinternen
„steeltomorrow“-Innovationswettbewerb zu den Gewinnern.
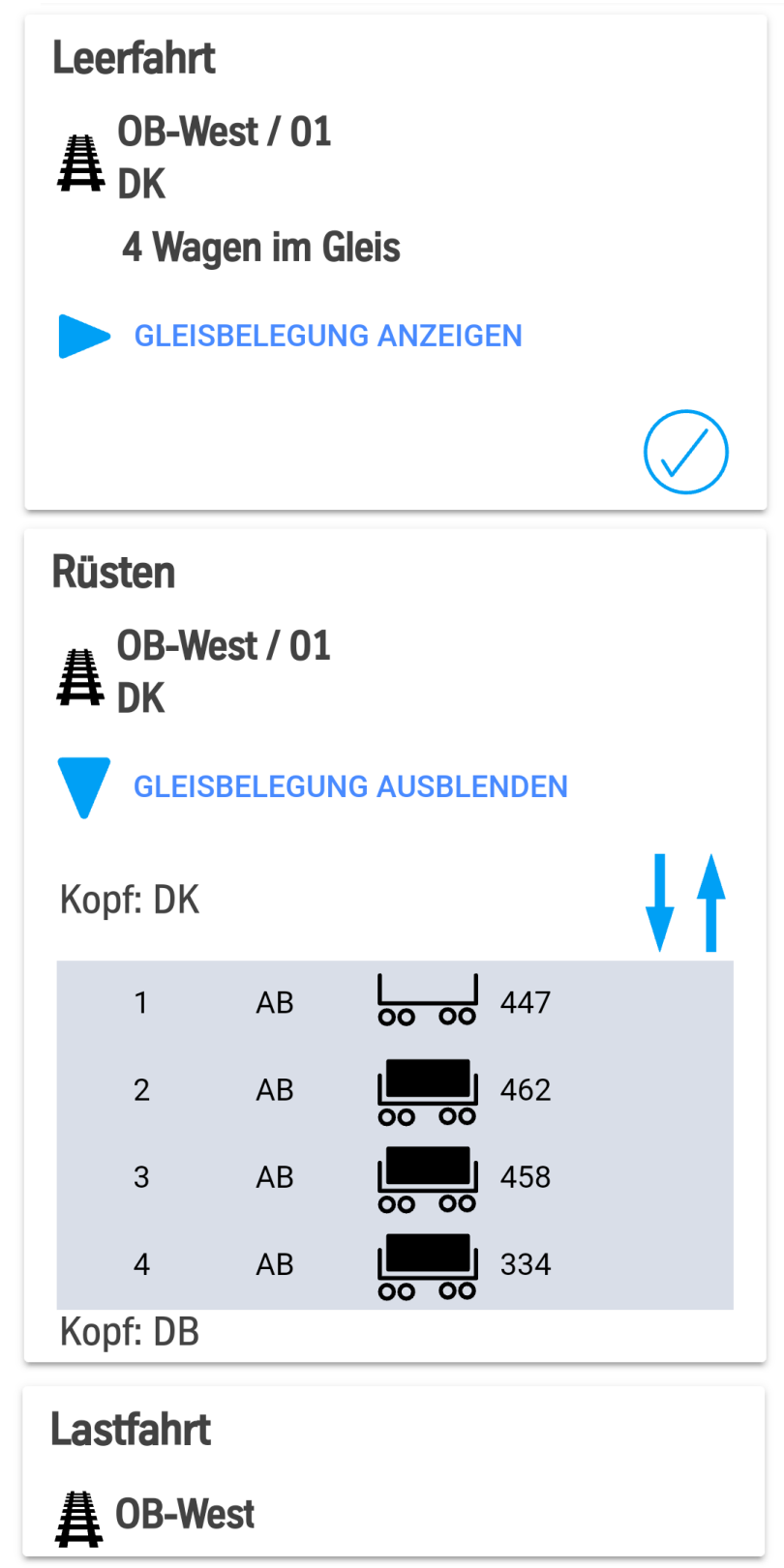
Die App vereinfacht die Kommunikation zwischen Lokführer
und Disponent.
Weiterer Puzzlestein der Roadmap Digitalisierung von
thyssenkrupp Steel
Die neue App steht stellvertretend für viele Initiativen,
mit denen thyssenkrupp Steel die digitale Transformation
gezielt und konsequent vorantreibt. Dafür bündelt das
Unternehmen Digitalisierungsaktivitäten über alle
Bereiche hinweg und stärkt kontinuierlich die digitalen
Kompetenzen im Unternehmen. thyssenkrupp Steel steigert
durch solche Lösungen beispielsweise die
Produktionsperformance, integriert die
Wertschöpfungsketten im Unternehmen und erhöht darüber
hinaus die Sicherheit der konzernweiten
Digitallandschaft.
|
Die Fehler der Vergangenheit
|
Wütende Aktionärer,
Stahlarbeiter mit Ängsten
Duisburg, Februar 2020 - Die Spannbreite der
wirtschaftlichen Sorgen bei thyssenkrupp ist breit
aufgestellt. Schon der abgelöste Konzernchef Kerkhoff
hatte im Herbst 2019 den Zorn der Aktionäre deutliche
vernehmen müssen.
Der aktuelle Sparzwang bei den tiefroten Zahlen
verunsichert und ärgert zugleich, da ein Missmanagement
zur eklatanten Kostenexplosion von fast 4,5 Mrd. Euro in
Investitionen im Ausland zum Ausbluten der heimischen
Werke führt. Und die im Herbst 2019 neue Vorstandschefin
Martina Merz hatte nach nur dreimonatiger Amtszeit mit
ihren klaren Aussagen, dass die aktuelle Lage ernüchternd
sei, das ein Verlust von nun 372 Millionen Euro (2019 60
Millionen) und einer Nettoverschuldung von gut 7 Mrd.
Euro bei einem geschrumpften Eigenkapital von etwas unter
2 Mrd. Euro zum puren Entsetzen beitrug. Auch der nach
dem Aus von Pramal Desai neue Stahlsprtenchef Bernhard
Osberg
Bei der Belegschaft geht die Angst um den Job um. Die IG
Metall nimmt kein Blatt mehr vor den Mund und Duisburgs
OB Sören Link stellt sich beim vom Aus bedrohten
Grobstahlwerk in Duisburg-Hüttenheim hinter die
Belegschaft und fordert klare Aussagen der
Verantwortlichen. Echtes Entsetzten hatte sich bei den
HKM-Mitarbeitern breit gemacht, als am Donnerstag (13.
Februar) durchsickerte, dass entweder ein Verkauf für
Hüttenheim - wie bei der gut agierenden Elevator Sparte -
oder das Aus im Juni 2020 drohe. Also keine dringend
notendigen Investitionen oder die eine vor Jahresfrist
angedachte Fusion mit Tatra um am Weltmarkt
konkurrenzfähig zu bleiben.
Nun drohen mehr als 200 0Stahlarbeitern im
Warmbreitbandwerk in Bochum und rund 800 Mitarbeitern
beim Hüttenheimer Werk in Duisburg durch den Sparzwang
der Arbeitsplatzverlust.
|
Innovative Rohstofftrocknung bei thyssenkrupp Steel
|
Duisburg, 30. Januar 2020 -Das
Duisburger Werk von thyssenkrupp Steel ist der
fünftgrößte Stahlstandort der Welt. Ein solches,
integriertes Hüttenwerk steht nie still. An 365 Tagen
wird rund um die Uhr gearbeitet. Tagtäglich werden im
Hafen von thyssenkrupp Steel in Duisburg enorme Mengen
Rohstoffe angeliefert – vor allem Eisenerz und Kohle für
den Einsatz im Hochofen. Diese Rohstoffe müssen
aufbereitet und der Produktion kontinuierlich in bester
Qualität zur Verfügung stehen.
Idee von zuhause in den Betrieb
überführt
Greifer heben die verschiedenen
Stoffe aus den Schiffen, damit sie im Werk weiter
transportiert werden können. Weil alles unter freiem
Himmel stattfindet, macht Regen den Greifern hin und
wieder einen Strich durch die Rechnung: Manche Stoffe
sind so fein, dass Nässe das Material in Schlamm
verwandelt. Ein Verladen mit den Greifern wird dann
unmöglich.
Weil das Trocknen des Materials lange dauert und der
nächste Regen oft schneller ist, haben die Ingenieure von
thyssenkrupp Steel nach Lösungen gesucht – und sind bei
den Kleinsten fündig geworden.
„Wir brauchen eine chemische
Lösung, um die Erze schneller zu trocknen“ – Das war der
Auftrag, mit dem sich der Chemiker Dr. Stefan Wienströer
und sein Team der Sache annahmen. Gleich zu Beginn kam
dem Vater von zwei Kindern eine Idee: Windeln. In denen
wird üblicherweise Natriumpolyacrylat eingesetzt, um
Flüssigkeit aufzunehmen. Der Stoff gehört zu den
sogenannten Superabsorbern: Kunststoffe, die in der Lage
sind, ein Vielfaches ihres Eigengewichts an Flüssigkeiten
aufzunehmen.
Arbeitsaufwand und Kosten
reduziert
Deren Einsatz erwies sich auch
im Hafen als goldrichtig: In mehreren Versuchen bewies
das Team gemeinsam mit dem Rohstoffeinkauf, dass sich die
Technik nahtlos in die bestehenden Abläufe integriert –
ohne Qualitätsverlust bei den Rohstoffen. Gleichzeitig
verbesserten sich Logistik und Kosten des Hafenumschlags.
„Statt Tage oder Wochen auf das
Trocknen zu warten, nutzen wir jetzt bei Bedarf die
Superabsorber. Ein Greifer mischt diese unter, danach
sind die Rohstoffe binnen zwei Stunden transportfähig“,
stellt Stefan Wienströer zufrieden fest.
„Ein verlässlicher Produktionsfluss ist in einem integrierten Hüttenwerk
der entscheidende Faktor. Wir können mit unserem Ansatz
an einer wichtigen Stelle für mehr Prozessstabilität
sorgen.“
Freuen dürfen er und das Team
sich nicht nur über den operativen Erfolg ihrer Idee: Im
Dezember 2019 gewann das Team mit dem Projekt auch den
Wettbewerb „steeltomorrow“, mit dem thyssenkrupp Steel
jedes Jahr interne Innovationsprojekte auszeichnet.
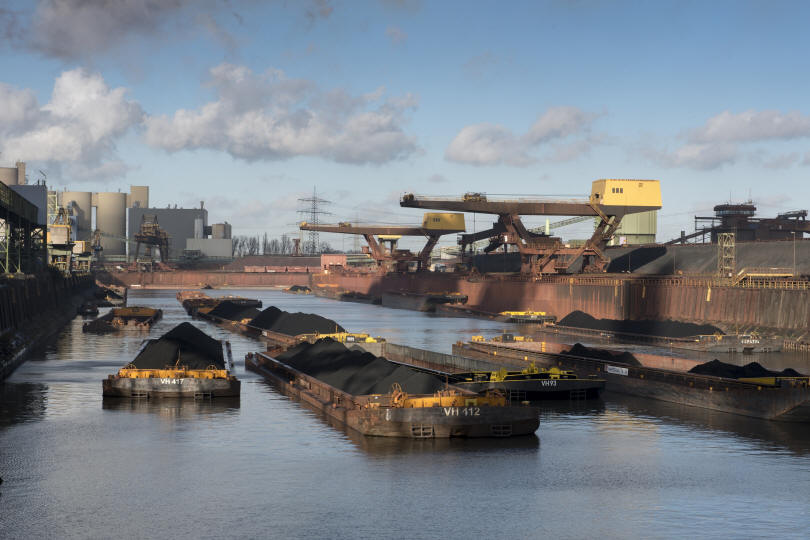
Im Hafen von thyssenkrupp Steel in Duisburg - Foto
thyssenkrupp Steel - werden täglich enorme Mengen
Rohstoffe umgeschlagen – insbesondere Eisenerz und Kohle
für den Einsatz im Hochofen.
|
|
|